Similar to how the 200-plus bones in the human skeleton provide the crucial support bodies need to function optimally, a wide variety of carts, workstations and storage units also provide the vital support healthcare facilities need to function at their best. In operating rooms, patient rooms, central services, intensive care units, environmental services, emergency rooms, and other areas, healthcare workers depend on all sorts of storage and transport equipment to treat and care for patients. Today’s technology also makes it possible to employ seamless inventory management, accurate cost-capture, manage medication, identify product usage and clinical trends using analytics, achieve regulatory compliance and infection prevention protocols, and more.
“Innovation and new products continue to emerge, increasing the choices that hospitals, clinicians, physicians and procurement professionals have, making storage space more valuable than ever,” said Rob Sobie, Worldwide Vice President , General Manager, BD Pyxis Supply Solutions. For example, “the changing regulatory environment and the recent Universal Device Identifier (UDI) mandates have increased the need for secure inventory tracking and tracing. The demand for data surrounding medical supply usage has increased exponentially over the last decade to help leverage contracts, make informed buying decisions, determine par levels, reduce stockouts and improve outcomes.”
Here’s a look at some of the items available today that can help healthcare workers in various disciplines address those and other issues while keeping themselves, their patients, and their facilities safe, satisfied, and solvent.
Meeting multiple needs
BD’s open and secure Pyxis Supply Solutions, now in its fifth generation, offers RFID capabilities and other contemporary components that empower users to meet various goals including UDI compliance, documentation, order and billing accuracy and more. “Connected to the hospital information systems, the BD Pyxis SupplyStation device is available with convenient touch-to-take or RFID-enabled technology that creates new data with every transaction that can be used to prevent stockouts, improve service and reduce the time clinicians spend in the supply chain process,” explained Sobie. “Regardless of the size of the facility or the area served (ICU, Cath Lab, OR, nursing units, etc.), the clinical and operational benefits, including improvements in documentation accuracy and regulatory compliance along with reductions in stockouts and time spent in the supply chain, are the most obvious. Easily overlooked, however, are the underlying financial gains from the Pyxis system placement which are quite tangible including reductions in annual spend and inventory levels, lower labor costs and improvements in revenue recovery. Combined, this unique system helps improve workflow, save money, protects budgets and ensures a very positive return on a unique and competitively priced investment.”
Meds near the beds
Gone are the days when clinicians have to walk back and forth between patient rooms, locked storage units, and prep areas to retrieve and dispense medication. With the right equipment, clinicians can do all of these activities at the point-of-care which can save time and improve care significantly.
“Decentralized medication storage units save clinicians significant steps and reduce stress,” said Mike Cook, VP of Sales and Marketing, Carstens, Inc. He says some of the features that clinicians also want are electronic keypad locks, RFID locks with auditing capability, employee-badge security access, and adjustable shelving to accommodate various medications and supplies. They also need ideal infection control properties for easy, optimal cleaning and disinfection. A new-generation Carstens product, launched last year, satisfies those needs.
“The WALLAroo 53250 Series is the perfect sized unit for storing medications for one or two patients at the point-of-care,” said Cook about the unit, which measures 20.2” wide, 26.2” high and 6” deep and comes with adjustable shelving. “When open, the door turns into a handy work surface, which makes it great for prepping medications or taking notes on a laptop,” he continued, noting its durable, quiet, and easy-to-clean design. “It is made from powder-coated steel, opens and closes with a quiet gas cylinder, and the surfaces are smooth for easy cleaning to help prevent the spread of bacteria. The finish is chemical resistant so it will not be damaged by the use of bleach or cleaning solutions.”
The WALLAroo comes in different woodgrain and solid color finishes with a choice of three lock options, including an electronic keypad, and an RFID badge access lock with audit trail capability. The WALLAroo now has a slanted top that helps prevent dust buildup and stops people from using it as a shelf — a new design feature based on customer feedback. Cook also pointed out that the WALLAroo can help reduce medication errors.
“The cost of a single medication error is enormous; and the cost of wasted clinician’s time is also very significant,” he said. “The WALLAroo 53250 helps prevent errors by storing medications and supplies where the clinician needs them to be. This has been shown to reduce the incidence of an error, and saves a sizeable number of clinician’s steps so that their time may be used more effectively.”
The two-bin win-win
For departments that appreciate the convenience and efficiency of a two-bin storage-inventory system — clean supply rooms on patient floors, and in surgery, emergency, and in other patient support areas — InterMetro Industries just launched the qwikSLOT Two-Bin and the two-bin Starsys system in May and June respectively. In describing the appeal and necessity of these units, Dave Salus, Healthcare Market Manager, said, “Having the right amount of supplies on hand, and making them easy to find and easy to identify what needs replenishing drives confidence in the process, reducing hoarding, increasing patient care time, reducing supply management replenishment time, and increasing supply management’s service capacity.”
Those are certainly the factors that can positively impact overall operating costs, as well as staff and patient satisfaction and safety, but it also takes considerable forethought, research and careful strategic planning to reap the full benefits of the two-bin system. Salus explains further: “To establish a successful two-bin process takes months of planning, reviewing SKUs, usage patterns, required quantity, the time it takes to replenish and not to mention the space required,” he asserted. “As part of this lean process the type of shelving should be considered, what depth shelf? Does it slant? And the space required — are you limited by existing storage space? Have you evaluated what could be available (i.e., can you create additional storage space by removing old cabinets that are underutilized or no longer really used)? Does some renovation need to be factored in and added to the timeline and budget?”
As for the new Metro systems, the qwikSLOT’s flexible slotted posts make it easy to readjust or reconfigure shelves to accommodate changing supplies and slanted-shelf options maximize storage space and increases visibility — something busy need and appreciate. Salus says coupling the qwikSLOT features with clear bins and color coding options will drive added efficiency.
For storing urgent supplies or items needed in high-use areas, the Starsys Two-Bin system is a suitable choice that can be located outside the supply room for fast access. “It is a solution for easily accessing supplies that require a level of contained protection due to their proximity to common areas, like the emergency department or to procedural areas, like in the operating room or sterile core,” said Salus.
Taking control of controlled substances
Innovation in storage and dispensing systems are also putting an end to stockouts, inventory discrepancies, and blind-count errors for controlled substances. Len Hom, Senior Product Manager, Omnicell, paints a vivid scenario of what can happen when facilities forgo today’s technology and stick with antiquated routines.
“Typically, controlled substances are stored in locked, medication specific bins within the automated dispensing cabinet (ADC). Nurses are asked to remove the medication from the bin and also are required to do a count of the medications that are in the bin, before closing the bin. Nurses are often hurried and human errors do occur. If the count is off, and it can happen with subsequent med removals by different nurses, this leads to inaccurate inventory accountability and inaccurate restock quantities. This can lead to missing doses and inventory stock outs. Additionally, if inventory counts are not accurate, par level optimization for each item will be a challenge.”
Some would consider that process risky, inefficient and costly. Omnicell’s controlled substance dispenser (CSD) replaces old rituals with a faster, more precise system for managing controlled substances with access to one dose at a time only, in the exact quantity prescribed for the patient. “Because the nurse is not opening a bin with multiple doses, there is not a requirement for the nurse to perform a blind count, when using CSD,” Hom explained. “This makes nurses more efficient by reducing a step in the med administration process, but eliminates the pitfalls of human error in counting, resulting in accurate inventory data which leads to the reduction in missing doses and stock outs.”
The Omnicell XT also features metal, locking-lid drawers which, unlike other models that are designed with plastic lids (which are easier to tamper with), keep all controlled substances completely hidden from view. The system also tracks and logs every user interaction. “For example, if a nurse is directed to an unlocked bin location through our guiding lights, there is no reason for a nurse to attempt to open or access a different bin location within the drawer,” said Hom. “The only bin that the Omnicell system unlocks is for the medication that has been approved by pharmacy and prescribed by the physician. If the nurse tries to open a locked bin, the nurse will not be able to open the bin, but Omnicell logs this activity for future analytics.”
Another important advantage over an ADC system is having accurate, on-the-spot automated labeling of syringe medications. Instead of filling doses from a vial and manually labeling those doses, which Hom says often doesn’t happen, “Omnicell XT cabinets have an automated medication label printer that can be configured to automatically print a label that meets all ISMP standards and protects the nurse and patient by properly labeling the syringe. It can also include the product bar code for scanning at the bedside in the bedside barcode med administration (BCMA) system.” XT offers a universal cassette for oral solids within the new CSD unit, new sensors to detect potential dispensing errors in CSD, and a new Starbus architecture to support wireless refrigerator locking and compartments for returned medications. “This maximizes hospital flexibility and can reduce costs to implement Omnicell systems,” suggested Hom. “Technologies such as RFID and refrigerated ADC locations now can be explored with our state-of-the-art Starbus architecture.”
On-the-spot supplies
Not every healthcare environment — or clinician — benefits from having a fixed, overhead or base cabinet structure, especially busy outpatient clinics. These healthcare providers might want more flexibility and opportunities to bring medical supplies to the point of care quickly and easily. Mobile cabinets are the solution, especially for stocking and dispensing high-use items such as gauze, bandages, lubricants and devices for certain in-office procedure. Using a mobile treatment unit means never having to leave the patient’s side to find and collect these items.
Michael Couch, Senior Marketing Manager, Midmark Corp. points to something else that some caregivers and healthcare purchasing teams may not have thought of before. “Another issue many of our customers faced with their built-in cabinets, particularly those located overhead, was the amount of wasted or unused storage space,” said Couch. “Caregivers of certain stature are unable to see or reach items in the furthest reaches of the overhead cabinets. The result is the back half of the cabinet goes unused.”
Midmark mobile treatment cabinets, part of the Synthesis Casework Collection, provide solutions for these and many other challenges. Technology integration, for example, is a must-have feature as accessing electronic health/medical records via computer tablets is now a ubiquitous event during patient-caregiver interactions and today’s mobile units must be able to accommodate these activities smoothly. “These workstations need to enable organizations to easily bring digital information to the point of care without sacrificing workflow or negatively impacting the caregiver or patient experience,” said Couch. “For instance, workstation options should enable caregivers to conveniently access patient information while allowing them to retain eye contact with the patients.”
Couch said the Midmark mobile cabinets also have a medical-specific design and are made with materials that can “deal with the rigors of a medical environment, such as the cleaning protocols needed for the medical space. Seamless panels and polystyrene drawers eliminate points of infection where bacteria can infiltrate — elimination of seams from high- touch and high-use areas help support good cleaning protocols.” Also, the units are built to accommodate facility expansion, support future procedures and technology at the point of care, and last but not least, they’re stylish. “While Midmark strives to provide products that enhance workflow and efficiency, we are also aware of the need to provide facilities with products that enhance patient comfort and engagement through the use of finishes that utilize calming color tones and wood finishes that tie into the overall look and feel of the facility.”
Mobile assurance
When a hospital expands, as so many do, sometimes the storage solutions that worked well before become more of a burden than a help. Holly Phillips, Communications Manager for Akro-Mils describes such an event and what one facility did to make the process easier.
“Previously the hospital used shelving and louvered panels attached to the walls; when the hospital expanded, adding two floors of ICU, they had to move supplies to a new area,” recalled Phillips. “They were forced to unload supplies from the shelves and panels, temporarily store them on a cart, move them to the new location and then reload them when the shelves and panels were reassembled in the new area.”
The solution: They brought in Akro-Mils mobile louvered racks with dollies and eliminated those time-consuming, extra steps since they were able to transfer all supplies to a permanent storage and roll it away to the new location. “In addition, by not having to attach panels and shelving they could avoid damaging the walls in their brand new facility,” said Phillips. “With constant expansion and rearranging departments, they have saved countless hours of moving supplies. With the dolly’s swivel casters and brakes, the loaded bins can be moved to where the supplies are needed.”
The system meets The Joint Commision Standards for minimum distance from the floor and ceiling and Phillips said, “this minimum height clearance was established to prevent contamination. The racks can be unlocked and moved for mopping the floor and then put right back in place. In addition the bins can be used to color-code like supplies, giving the staff visual cues to easily find what they are looking for. The supplies themselves are openly displayed, not hidden away in a box or drawer. They rolled out the color-coding system department by department throughout the hospital. The staff love the bin system.”
More than an exam table
Much the way the platform bed with drawers underneath provides a handy two-in-one bonus for bedroom furniture shoppers, the Brewer Company’s 6801 Exam Table is as much of a space-saving storage product as it is an exam table for clinicians, especially those working in tight quarters, says OpenMarkets co-founder and Senior Vice President Tom Derrick.
“The unique, one-of-a-kind 6801 High-Low Exam Table is an innovation in storage,” said Derrick. “This product incorporates pass-through drawers and a pass-through work surface. The drawers are in effect an added on storage cabinet accessible on both sides. All of these features are built into the Exam Table.
“This saves a ton of space in any tight patient-care area and may eliminate the need for any additional storage cabinets or carts,” he continued. “The work surface is an improvement on the standard “mayo stand,” in that it is directly tied to and in line with the patient’s seat, allowing the clinicians to use their laptop, charts and materials while facing and speaking with the patient.”
Remedies for SPDs
Sterile processing professionals, under incredible pressure to turn over instrument cases faster than what seems possible, also appreciate having the supplies they need nearby instead of engaging in the time-consuming task of walking through isles of carts or needing to bend and get on a ladder to retrieve items several times a day.
“The easy answer is to eliminate the time spent walking and searching, and deliver supplies to one location,” said David Phillips, Marketing Manager, Hänel Storage Systems. “If it takes 60 seconds to find one item by a technician searching for it, and 40 seconds to have it delivered to the technician, the 20 seconds saved will add up. Surgical containers, wrapped sets, implants, instruments and other types of supplies can be stored in a single location, using a variety of easily identifiable shelves, bins and drawers.”
Hänel’s inventory management options include first-in, first-out (FIFO), expiration dating and lot number that are detailed by the Association for the Advancement of Medical Instrumentation (AAMI) and sterilization standard ST79. “Managing inventory in these ways can improve inventory accuracy to nearly perfect levels, which reduces overstocking, shortages and expired items,” said Phillips, adding also that employee health and well-being should also be at the top of every manager’s list. Not only is it important for the technician’s sake but injuries and lost productivity hurts a facility too.
“Surgical trays must be a maximum of 25 pounds, and that weight can feel much heavier when it must be brought down from a top shelf, or picked up from near the floor,” said Phillips. “When such extending or bending is done repeatedly, it can easily result in an injury. According to OSHA, the ‘golden zone’ for lifting is close to the body, between the waist and mid-chest height. Comparable to the strike zone in baseball, this area is where the arms and back can lift the most weight with the least amount of effort. Hänel developed the Rotomat vertical carousel to expose workers to the least possible amount of physical stress. Surgical supplies are kept in a central location, rather than having them spread across countless carts. The ergonomically-correct access point eliminates bending, stooping, reaching and the use of stepladders. The Rotomat allows surgical trays, instruments and supplies to be accessed within OSHA’s golden zone, and the only movement made by hospital staff is the side-to-side, lateral transfer of items from storage to a case cart bound for the OR. He says SPDs that adopt the system can increase production by as much as 33 percent.
Finding the best way to clean and store scopes is another huge concern in recent years, and ever since major regulatory bodies released newer, stringent guidelines for scope reprocessing, Mark Roberts, Product Development Manager, LogiQuip, says his company has been engaging with sterile processing departments much more frequently. “If a facility wishes to be compliant they must make changes,” said Roberts, whose company supplies a variety of medical equipment including endoscope storage cabinets. “While the cleaning process offers the greatest opportunity for the support of infection control, the storage segment does play a role.”
So, how does LogiQuip scope storage technologies help in the effort to reduce the spread of bacteria?
“From a technical aspect, customers are interested in our tracking feature that ensures scopes do not exceed their allowable hang-time in clean storage,” explained Roberts. “For a few years now customers have seen the benefit in the positive pressure HEPA feature, but are now exploring our channel purge system which dries the interior of the scopes. I think this is of tremendous value in supporting infection control as this is eliminating the remaining bacteria-causing moisture. We’ve seen several examples of water spraying out of scopes that were connected to channel purge in spite of the fact they had been hanging in cabinets with ambient ventilation for days.”
The upgradable cabinets offer other features as well, including grade 304 stainless steel structures that won’t rust or flake, a certified HEPA system that exchanges air more than 100 times per hour, lab-tested temperature balance in and outside the cabinet, and a newly upgraded, quieter air pump.
“Another recent upgrade was with our Endotrack technology package. With this, we provided the ability to add or delete employee badges using the cabinet’s scanner to eliminate wasted time interfacing with a separate computer,” said Roberts, adding that options also exist for facilities with limited budgets and space. “A facility can start with our ambient cabinet, later move into the positive pressure feature, then our channel purge system, and eventually add-on our technology package that tracks hanging time and controls access,” he said. “We also understand the cost of floor space, and so we have a range of product to meet particular needs.”
A fix for pharmacy
For those working in the pharmacy, Shane Mummery, President, H+H System, Inc., says most are seeking storage solutions designed with reliable features that satisfy specific safety and workflow concerns.
“Many Hospital Pharmacies have found that their old setups for storage are inadequate or disorganized, having been adapted from an older design and then added onto without an overall plan for workflow and storage,” said Mummery. “A lack of organization can cause drugs to be put into the wrong bin, spill over into other bins. Confusion on placement of bins can cause the wrong item to be picked.” Other concerns have to do with expansion, standardization and regulatory compliance. “Many pharmacies are experiencing growth and an ever-increasing amount of items they must store locally,” he said, adding “cleaning and sterilization is always an issue but even more so with new regulations and guidance documents coming in the next 18 months.”
H+H FlexShelf Systems and Customized Divided Trays are the company’s two main categories with both highly focused on space efficiency and organizational features that can support multiple and changing needs throughout the pharmacy workflow. The products are designed to fit any space and function.
“H+H FlexShelf saves at least 30 percent space since they are so highly flexible,” Mummery asserted. “By maximizing the space on every exchange unit, picking station and storage columns, pharmacies can decrease the number of drawers and trays, and can maximize floor and wall space. Our Flexible Divided Trays fit the majority of name brand carts (e.g., OmniCell and Pyxis) and can be customized to organize medications. Security features such as bags, tearaway seals and locks and locking lids keep meds safe and clean. Color options are available on all trays and this feature is ideal for coding trays by departments or functions.”
The H+H FlexShelf materials are also durable, resistant to corrosive chemicals and can be cleaned and disinfected safely using most commercial products. “Dust caps are also available for H+H FlexShelf units to provide smooth cleanable surfaces and resistance to dust and dirt ingress from collecting in screw caps and connectors, which is especially important for use in Clean Rooms.”
Fetching food carts
There are also a lot of factors for food service departments to consider when selecting ways to transport and provide meals to patients. What seems to be the biggest concern among food service managers is that meals tend to be cold by the time they reach the patient. Whether serving patients in acute care settings, affiliated rehabilitation centers, palliative care or residents in skilled nursing facilities, the vast majority will find cold food unappealing and leave most, if not all of it, on the tray. The wasted food and money is obvious but it can also affect patient health and nutrition negatively. Nutritional deficiency is a significant problem for many hospital patients, even more so among the elderly. Patient satisfaction scores are also on the minds of every healthcare provider today as well — serving cold, pre-portioned meals on institutional trays certainly doesn’t help.
Conversely, by letting patients choose what kind of food they prefer and how much of it they would like and then plating it up hot and fresh right on the spot might be the better way keep patients nourished and satisfied. That’s exactly what 600-plus healthcare communities across North America are doing with the Lakeside SuzyQ Cart System. Inventor Suzanne Quiring, CDM, Registered Dietitian, says facilities are experiencing “excellent results: high meal satisfaction, hotter food, less food waste, significant dollar savings and increased direct connection with the Food Service team members. The SuzyQ cart by Lakeside is the vehicle to bring hot meal choices to the residents, and allow them the daily opportunity to say ‘if’ and ‘what they would like to be served, before anything is platted and put down in front of them,” said Quiring.
The system can accommodate meals for 20-40 people and a smaller model, the mini SuzyQ, feeds 10 to 20. Quiring says the purchase includes staff education support with webinar classes, staff training manual, and email and telephone support from a Registered Dietitian with 25-plus years experience in Residential Care Food Service. “The ROI is easily achieved within one year with less food waste and improved production numbers, and many Health Care Communities report a reduction in 30 percent to 50 percent less food waste when moving towards table side dining service with the SuzyQ cart,” she said, adding that a small nonprofit recently saved $90,000 using just one cart and put those savings into paying for additional staff hours.
About the Author
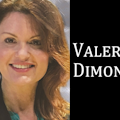
Valerie J. Dimond
Managing Editor
Valerie J. Dimond was previously Managing Editor of Healthcare Purchasing News.