Making do with much ado by award-winning Supply Chain teams
Crises and disasters tend to draw out the best or worst of people as evidenced in their initial reactions and ongoing responses to what happened. A global pandemic that not only infected millions of people, but also proved fatal to hundreds of thousands, drained the supply chain of available stock and cast a pall on its reputation, is no exception.
The COVID-19 coronavirus afflicted all healthcare organizations universally – large and small, urban and rural, decorated and striving for recognition.
As a result, Healthcare Purchasing News wanted to share with readers what top-flight, award-winning organizations have been doing and thinking as they navigate through the ongoing crisis. HPN reached out to all 17 of the organizations that have earned “Supply Chain Department of the Year” recognition and status since the launch of the award in 2004.
Not surprisingly, many were swamped and engulfed in meeting the daily and accelerated demands and needs of caring for patients. Yet roughly half volunteered some of their busy time to share their insights on the challenge(s) the team faced, the solutions the team designed to achieve the desired outcome(s) and who was instrumental in the process. In random order chronologically, here’s what they shared.
Organization: Geisinger Health, Danville, PA
Supply Chain Department of the Year: 2008 (No. 5)
Joe Goyne, Senior Director, Logistics, Supply Chain Services, Geisinger, Wilkes-Barre, PA
Challenge(s) faced: Geisinger transitioned its prime distributorship in late summer 2019. As in any distributor conversion, we proactively planned for this transition to avoid the potential for stockouts or supply disruption by ensuring adequate supply on hand. The timing of this transition ultimately affected our allocation allotments that were set by the manufacturers and distributors who were using utilization reporting from the time period not reflective of true demand.
Solution(s) delivered: Identifying the root cause for variances between allocation availability and forecasted demand allowed the team to identify gaps in product availability and alert our strategic sourcing team as to the need to proactively mitigate the impact caused by the situation. We also leveraged our supplier partners and GPO to identify opportunities to participate in “spot buys” to offset additional demand needs. Also, a “non-traditional” sourcing checklist was developed to engage new partners for sourcing high demand, hard-to-get supplies as the market tightened. We successfully navigated these new markets.
Influential, instrumental leaders: Inventory Control, Distribution Center, Strategic Sourcing, Prime Distributor (Medline) and Group Purchasing Organization (Premier), Legal and Finance.
Organization: M Health Fairview, Minneapolis
Supply Chain Department of the Year: 2017 (No. 14)
LeAnn Born, Vice President, Supply Chain, M Health Fairview, Minneapolis
Challenge(s) faced: Our health system works with two different med/surg distributors because we have not yet integrated that service following the integration of our two legacy health systems. We were able to turn this challenge into an effective way of communicating and solving problems with sourcing through major product disruptions.
Solution(s) delivered: We set up daily huddles where M Health Fairview’s distributor representatives from Cardinal and Owens & Minor joined a variety of staff from Supply Chain to review what was needed, what was ordered, in route, available to order, etc. Everyone has been creative together. This resulted in an incredible team that was able to set aside the competition that the two distributors might have known, collaboratively source products from the two distributors, direct from manufacturers and from alternative suppliers. For quite a while, these meetings were daily. We have reduced them now to weekly.
Influential, instrumental leaders: At moments in time, it expanded beyond Supply Chain to include Infection Prevention, Nursing Practice and Education, Quality and Clinical Operations, but the long-standing participants have been local representatives and leaders from Cardinal and Owens & Minor along with Supply Chain staff from our sites, purchasing, value analysis, data and analytics, leadership and more.
Organization: Piedmont Health, Atlanta
Supply Chain Department of the Year: 2018 (No. 15)
Joe Colonna, Chief Supply Chain and Project Management Officer, Piedmont Health, Atlanta
Challenge(s) faced:Determining a new usage rate on PPE products that suddenly became the most important and most-used items. We needed to know our total supply of these items in our distribution center and across all of our 11 facilities. We had to have real-time information to help us determine where we needed to move supplies around the system and a real-time report to show our command center. We were in a similar situation with ventilators and associated supplies. In addition, our suppliers suddenly became hit-or-miss on whether we would see our deliveries.
Solution(s) delivered:We instituted a daily physical count of all supplies and ventilators at the sites and the distribution center. This information was entered into a manual report that went to the command center. By watching what was being used at the sites and in what quantities, we began to estimate our new utilization rates. This allowed us to better predict where we would need to move vents and how quickly we would use our inventory of PPE. This also allowed us to provide better information to the command center. Working with our clinical leaders, we instituted this process to better manage our inventory and this helped keep product and equipment in the hands of our caregivers. The daily counts also helped us to keep track of product that was being supplied by the state or through donations. This product would not have been reflected in our ERP systems. Using this process, we ran low but we never ran out of needed supplies.
Tip – We never factored in what was “on order” into our estimates. While we were receiving products, there were no guarantees. We managed the inventory we had on hand. Numbers were adjusted as product was received and in real time.
Influential, instrumental leaders: I will simply say that this was indeed a team effort. Everyone stepped up in different ways and many took on non-traditional roles. I think that early on, everyone was surprised at the speed at which things escalated and how fast supplies became hard to find. I was pleased with the transparency of our partners at both Cardinal and Medline. They came through for us in many ways and were honest in telling us bad news. They also helped us in predicting some future shortages that allowed us some time to plan accordingly.
On the other hand, there were some bad actors out there, trying to sell at price-gouging rates, counterfeit product or no product at all. I will say that we may have paid more than we wanted in some cases but we avoided the real scams. There is a special place in hell for the people that tried to profit from this pandemic and an even lower level for those that stole providers’ money.
Finally, I will say that I have been in the Healthcare Supply Chain field for 30-plus years now and I could not be more proud of the Supply Chain professionals we have here at Piedmont. They worked very closely with our clinicians and leaders. They had to figure things out on the fly and with information changing, sometimes, hour by hour. They stood up to the challenge and worked long hours and many weekends to make sure our caregivers and patients had what they needed to do their jobs. They continue to stand up to the challenge, as our numbers increase for the second time. I feel the same way about all of the Piedmont Healthcare team members. There is not complaining, there is compassion. Everyone is in this together. The goal is taking care of the patients as safely as possible for the caregivers. I am so very proud to work here.
Organization: Terrebonne General Medical Center, Houma, LA
Supply Chain Department of the Year: 2004 (No. 1)
Kathleen Gathers, Director, Supply Chain, Terrebonne General Medical Center, Houma, LA
Challenge(s) faced: The most challenging issue we faced at TGMC was the feeling of helplessness. There wasn’t enough knowledge about coronavirus to know how to treat it at the time. We knew it was respiratory-related so we ramped up ventilators and supplies, and looked at creative ways to intubate using clear shower curtains to prevent the spread of the aerosolization. Hearing from our clinical staff, their recommendations, and then searching for solutions was our role. Another challenging area was the allocation process put into place by the distributors. While understanding the need for it, New Orleans and the surrounding area was a hot spot and the communication to us was that PPE wasn’t available because they needed to go to other hospitals that weren’t affected by COVID-19 at that particular time.
Solution(s) delivered: When COVID-19 started to make the news in January, we monitored what was happening worldwide. In February, we started to order a heavy supply of masks, gloves and gowns. We began to bulk-purchase other PPE and store in a small conference room, which grew into two conference rooms, and eventually a third floor that wasn’t utilized. We had 21 straight days in April where we ordered everything we could get our hands on and then placed orders on Saturday and Sunday thinking vendors were updating their online availability, and we didn’t want to wait until Monday morning. Being creative, [we were] thinking outside of the box and buying from vendors who we normally didn’t purchase from. For example, our regular disposable stethoscopes were backordered, so we found really inexpensive ones that needed to be put together. It was “all hands on deck,” and we have a great team in place who really stepped up to the challenge.
Influential, instrumental leaders: The entire Supply Chain Team at TGMC was fantastic – Darlene Grimes, PSD Manager, Tara, Debbie, Steve, Macy, Calvin, Bill, Vernon, Pat, Xavier, Annette, Vicki and Dominique. We had the support of our Administration Team and provided them with daily updates of inventory on hand for critical items. Everyone pitched in and asked, “How can I help?” and our team provided excellent customer service to our staff. Cardinal and S2S Global were great from a distributor perspective, but I need to mention McKesson Medical. Not our regular acute care supplier, but our rep Johnny Bordes was extremely helpful in pushing orders through.
Looking ahead, we have taken a “count on yourself” type of thinking when it comes to PPE/supplies. Our hospital may have decent supply right now, but not knowing what the future holds, continuing to see shortages, having to rely on product coming from other countries, and [seeing] hospitals all trying to purchase the same supplies, [we know this] is not going to end anytime soon. We must continue to make sound decisions, keep lines of communication open with distributors, but at the same time become accountable and self-sufficient.
Organization: Tower Health, West Reading, PA
Supply Chain Department of the Year: 2019 (No. 16)
Rita White, Vice President, Supply Chain, Tower Health, West Reading, PA
Challenge(s) faced: The COVID-19 pandemic created critical supply shortages that impacted healthcare systems across the globe. As a result, supply chain teams faced such challenges as increased allocations on critical supplies and a lack of reliable ETAs for incoming product. Sourcing paths typically relied on were compromised, resulting in a significant reduction of the availability of critical supplies at the same moment both the demand and the significance of the need peaked. Standard processes were unable to meet the challenge of the extraordinary circumstances, requiring new processes be defined and incorporated virtually overnight. Additionally, standard critical product became increasingly difficult to obtain, requiring new functionally equivalent products be identified, reviewed, and implanted as clinically acceptable substitutes. As these challenges were being addressed, the healthcare supply market was flooded with “false” vendors, who presented offers of supplies at exuberant prices for supplies that frequently arrived damaged or did not arrive at all.
Solution(s) delivered:In the early weeks of the COVID-19 pandemic, Supply Chain’s focus was directed toward preparations and coordination with internal stakeholders and partner vendors. We ensured we were ordering to our maximum levels for all supplies under protective allocation, began proactively ordering reserve supplies of anticipated impacted products not already on allocations, and set up an offsite warehouse to store additional inventory.
We also reached out to our department leaders and asked for assistance in identifying additional items that may be needed to support an influx of COVID-19 patients, and asked they identify their critical supply needs and project what their volumes may look like in a “surge” period. Throughout the entire emergency, we have stayed in very close contact with our Supplier partners, primary distributors including Medline and Fisher Scientific, and HealthTrust/Allspire GPO liaisons to stay informed regarding supplies at shortage risk.
As PPE and critical items were placed on allocation, Tower Health Supply Chain continued to forge relationships with new vendors while leveraging current ones to obtain available supplies. New vendors were evaluated and vetted through a series of standardized criteria. As demand forced manufacturers and distributors to place critical items on allocation, clinical and nonclinical teams partnered to identify, review, and obtain substitute items from multiple vendors, thereby expanding the inventory pool. Through these measures, Tower Health was able to maintain a continuous supply flow, even as shortages spread across the country.
Reporting became extremely important to our efforts in monitoring and tracking critical supplies throughout the supply chain. To support our needs, our team partnered with the clinical and IT areas to develop new reporting to track critical metrics around supply stock on hand, expected deliveries, average utilizations and items reaching critical shortage levels. Our inventory teams also implemented daily cycle counting seven days a week to capture timely stock-on-hand counts.
Influential, instrumental leaders:It truly has been an incredible journey with so many individuals exemplifying self-sacrifice and the truest commitment to our mission. No doubt, all those on the front lines, including the Supply Chain Inventory and Distribution staff, are exceptional and inspiring individuals who have risen to the occasion. So many of the Supply Chain team have worked tirelessly all hours of the day since the earliest onset of the crisis. Just as a few examples, I’ve had team members drop everything to race out to local retailers to hunt down urgently needed supplies, such as plastic shower curtains to be used as protective screens or temporary plastic hooks to hang isolation gowns for reuse. Others have spent countless hours following up on innumerable leads from traditional and nontraditional sources to find any that could result in a shipment of some critical supply. Our Purchasing teams are following up with vendors daily on the chance there will be some supply available to ship, tracking and following up constantly on open orders, sourcing alternate items, researching substitutes, vetting new vendors, and analyzing data to anticipate where supply levels are becoming critically low. It is not an overstatement when I say we have turned over every rock to find needed supplies to ensure colleagues have what they need to safely perform their vital roles.
The Supply Chain team has not gone this road alone. So many within Tower Health – from clinical team members, to support staff, to our incredible Administration – have worked relentlessly to ensure the well-being of our patients and colleagues. We have also had the privilege of working with incredible vendor partners. Medline, in particular, has been a true partner to us in navigating the challenges of this pandemic. Likewise, HealthTrust has demonstrated amazing support, providing additional sourcing opportunities and resources to keep us informed of the quickly evolving situation. We have also been so fortunate to have remarkable community support. So many within our local community, from area businesses to individuals, have come forward to provide assistance in the form of supply donations.
As Supply Chain professionals, we feel an overwhelming responsibility to ensure we are supplying our colleagues with what they need to effectively and safely care for patients. No other time in my career has there been a situation in which carrying out this function has been so challenging. I am honored and humbled to be part of this organization and to lead a team that has come together and stepped up in such a time of crisis.
Organization: UPMC Health, Pittsburgh, PA
Supply Chain Department of the Year: 2012 (No. 9)
Jim Szilagy, Vice President and Chief Supply Chain Officer, UPMC, Pittsburgh
Supply Chain-specific Challenge(s) faced:UPMC Supply Chain was faced with many challenges, such as market availability, border closings, increased pricing, and raw material shortages while meeting unprecedented product demand to ensure the safety of our employees and patients. Sourcing resources were tasked to deliver on their routine day-to-day activities as well meet the challenges posed by the pandemic – such as finding supply alternatives, expediting delayed shipments, managing the ripple effect of product availability, and restrictions and delays at borders that impact distributors and suppliers’ ability to meet contractual obligations .
Solution(s) delivered: In response to the inflated demand we designed, developed, and implemented a supply/demand forecasting platform in partnership with clinical and executive leadership. The new forecasting platform provides the following information to help inform operational decision such as employee and patient safety and surgical procedures:
- Quantity on hand (Warehouse)
- Calculated “Peak” Demand
- Days on Hand
- Outage Date
- Forecasted allocations and supplemental order volumes and dates
- Forecasted Supply Health Graphs
- Supply Health Indicators (Red/Yellow/Green) based off determined criteria
Influential, instrumental leaders:Supply Chain Leadership, Supply Chain Sourcing, Supply Chain Demand Planning, Supply Chain Logistics, Supply Chain Data Management & Analytics, Supply Chain Materials Management and Supply Chain PMO Group.
Pharmacy-specific Challenge(s) faced: COVID-19 rapidly stressed operational pharmacy and supply chain resources with a need to protect supply from disruptions in the global supply chain while also scaling up operations to meet the potential tsunami of critically ill COVID patients. Very few health systems have access to a full-scale, perpetual inventory system, so these types of supply challenges can be difficult to manage when inventory counts are being manually entered into one-off, excel-based tools that are prone to error and difficult to manipulate for longitudinal trending. We needed to create a more sophisticated supply monitoring tool to capture on-hand inventory quantities from 40-plus hospitals across a multistate integrated delivery and finance network to solve for the critical need to:
- Monitory daily inventory health of both drugs and PPE
- Model longitudinal supply trending
- Respond quickly and accurately to a detailed, NDC-level inventory request from the state of Pennsylvania
Solution(s) delivered: Within two weeks of development time, we designed, developed, and launched a web-based crisis inventory management platform in partnership with software engineers, pharmacists, and project managers. The platform includes the following features:
- Single-sign-on capabilities for enhanced security
- Mobile-enabled user interface for use in hospitals and inventory storage rooms without having to use a computer browser
- Configurable reminder notifications, drug and PPE lists
- Integrated NDCs and drug database information
- Business Insights-powered data modeling, trending, and visualizations
- Exportable data and reporting for sharing with government agencies
This process can now be configured to count and trend any shortage-impacted items, not just for COVID. We also provided the solution to other health systems so that they, too, could leverage the power of the web-based portal with integrated collaboration and reporting tools to monitor COVID-19 critical supply counts.
Influential, instrumental leaders: UPMC’s fully owned commercial supply chain data analytics spinoff, Pensiamo Inc.; UPMC’s GPO and Wholesale organization, HC Pharmacy; UPMC Supply Chain; and UPMC Hospitals, retail, long-term care, and repackaging pharmacies.
Organization: Vanderbilt University Medical Center, Nashville, TN
Supply Chain Department of the Year: 2014 (No. 11)
Teresa Dail, R.N., CMRP, Chief Supply Chain Officer, and President, Vanderbilt Health Purchasing Collaborative LLC, Vanderbilt Health Supply Chain Solutions LLC and Carefluent Connect LLC
Supply Chain-specific Challenge(s) faced: VUMC faced the same challenge as many organizations across our country, and globally, around the acquisition of N95 masks. Early on in the process, the standard vendor we utilize notified us that the primary mask we routinely purchased would not be available for an undetermined, but lengthy, period of time. As we began to look for alternative products, we recognized that we were going to need to begin to conserve our current inventory. As the COVID situation evolved, our anesthesia colleagues sought approval to wear an N95 for all cases requiring intubation with typically two providers per case. In addition, our surgical specialties began to ask our PPE approval committee to consider waivers allowing N95 usage for all providers in the room for very specific case types (trauma, ENT, pulmonary. L&D and others). Because pre-op testing was not even being contemplated at this time due to all elective cases being cancelled, it became evident that we needed to develop a plan, under Emergency Use Authorization, to allow us to maximize the use of the N95s.
Solution(s) delivered: The supply chain at VUMC reached out to colleagues at the University of Nebraska to discuss an initiative they had implemented around the use of UV light to effectively decontaminate, and therefore allow for reuse, of the N95 mask. After reviewing their process and data, this information was presented to our infectious disease experts for their input. Support was gained to implement this process at VUMC. The technology was not new to our EVS team, which utilizes these devices to clean specific clinical areas such as our burn unit. The concept of reprocessing was shared with the chairs of all the departments as well as our incident command and executive leadership. Once approval to proceed was received, we began work with our facilities management and environmental health and safety team to literally build out an unused area within the medical center to ensure a safe environment in which this initiative could be achieved.
A task force was established, including surgeons/anesthesia, infection prevention, sterile processing, perioperative leadership, environmental health and safety, quality and nursing education. [Standard operating procedures] and staff education were developed. A full communication plan for the perioperative team, as well as the organization, was developed and implemented. A plan was also developed to shift the management of the day-to-day issuing of new N95s to the perioperative clinical team. This was done to place ownership on the unit to drive compliance of reprocessing. UV decontamination was implemented initially in surgery in our adult and children’s hospital. It was then expanded to other units also utilizing N95s, including the emergency department and clinics. We also implemented and supported this process for one of our community hospitals. Once the FDA approved the use of hydrogen peroxide for decontamination, we shifted to use of our onsite sterilization devices at all sites.
Influential, instrumental leaders:[Including those listed above,] I would like to acknowledge Ten Med, which helped us quickly find and then provided an additional Skytron unit. The representative also worked to ensure proper training of our staff as the unit we purchased was different than the two already owned.
Organization: Dartmouth-Hitchcock Health, Lebanon, NH
Supply Chain Department of the Year: 2020 (No. 17)
Curtis Lancaster, Vice President, Supply Chain Division, Dartmouth-Hitchcock Health
Supply Chain-specific Challenge(s) faced: Understanding in real-time the quantity of PPE we had on hand and on order. Reviewing that data and then predicting which shoe would drop next, i.e., after masks, it’s gowns.
Solution(s) delivered:[We] gathered projected utilization from clinical stakeholders and built a supply and demand model that projected need by month. The model could be adjusted by anticipated surge levels as well. The model not only helped us anticipate PPE needs due to COVID, but also the requirements for recovery.
Influential, instrumental leaders: One, involving clinicians early to understand what we were doing and the information we needed form them. Two, our Incident Command Center served as the primary recipient of our model’s output; they could act based on our analyses. Three, making sure our Operations Team knew where everything was; we were sourcing and receiving PPE at unprecedented levels and finding places for it was challenging; we also opened a new warehouse dedicated solely to fulfilling the PPE needs of our hospitals.
Return to main story.
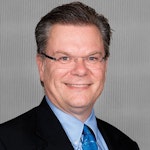
Rick Dana Barlow | Senior Editor
Rick Dana Barlow is Senior Editor for Healthcare Purchasing News, an Endeavor Business Media publication. He can be reached at [email protected].