Latest material handling tools, toys rev up the cool, drool factors
CHICAGO – If you haven’t seen some of the latest developments and innovations in material handling devices and equipment accessible to and enjoyed by every industry outside of healthcare providers then you’re missing a lot.
Thankfully, Healthcare Purchasing News attended Material Handling Institute’s (MHI) ProMat 2023 event here at McCormick Place in late March to provide you with a score of snapshots and synopses on the tools and toys that could season your storeroom(s) and warehouse(s) – or your consolidated service center. [Editor’s Note: See Buyline, HPN, May 2023 for the introduction.]
To borrow and adapt a slogan from that old Oldsmobile television commercial, “these are not your father’s material handling devices and equipment.”
Four years ago, which was the last time MHI held the biennial ProMat in Chicago (MHI alternates ProMat with MODEX each year) before the COVID-19 global pandemic-induced hiatus, distribution, logistics, materials handling and supply chain executives and professionals were wowed by collaborative robotic arms (a k a “cobots”) used largely for loading and unloading boxes on conveyor belts and pallets to trucks and vice versa.
Cobots may have been all the rage at ProMat 2019, this year the cobots returned in full-force but they took a back seat to something else that seemed to occupy plenty of booths on the show floor: Automated guided vehicles (AGVs) and autonomous mobile robots (AMRs) for inventory, logistics, materials handling, distribution and even cleaning and decontamination. While many AGVs and AMRs traveled by wheels, at least one walked on two legs as close to humanoid form as possible outside of Hollywood.
Aside from AGVs, AMRs and cobots, what turned heads and drew eyes at the show? Here’s a short list of nine additional attractions to complete the dynamic dozen:
- Traditional forklifts welcomed their high-tech and souped-up siblings, equipped with batteries for power; cameras and sensors and other visual aids for directional autodrive, facility mapping and safety; and forks that can maneuver 90-degrees to the left or right to accommodate narrow aisles between high vertical shelves
- Wireless battery chargers for AGVs and AMRs that obviate the need for tethering docks
- Wired and wireless integration and interoperability between cobots, robots and internal systems, such as inventory, logistics and warehouse management systems
- Vertical storage tower capabilities managed by robots
- Simulation modeling and programs for training forklift operators as well as designing warehouse footprints and layouts for efficiency, productivity and throughput
- Wearable automation devices for accurate picking and replenishment and inventory tracking, including computers on rings and wrists, gloves and eyeglasses
- Exosuits for a variety of ergonomic reasons, such as reinforcing posture and relieving stress, and not necessarily confined to the storeroom or warehouse either
- Drones for inventory tracking and tracing as well as footprint monitoring as storage options expand in height, length and width, and can offer more convenience and flexibility than human views from vertical lifts
- The science behind selecting the optimal totes for picking and storing products
Cobots and robots to go
From large booths to small booths, endcaps to inside aisles, scores of exhibiting companies demonstrated collaborative robotic arms (cobots) that grabbed or picked up boxes using rubber grapplers or vacuum suction for loading and unloading cargo containers, tractor trailers and conveyor belts to stacking on AGVs and AMRs for transport.
Even more exhibiting companies showcased AGVs and AMRs – whether programmed or remote-controlled via computer console or tablet – moving stock between points, navigating around obstacles and people. At least one concentrated on cleaning.
During an exhibit hall educational session on the show floor, Adam Kline, senior director, Product Management, Manhattan Associates Inc., strove to temper “robomania” with practical and realistic observations and responsible usage in his session titled, “Man & Machine 2.0: Prioritizing People in a Robot World.”
Kline acknowledged that interest in and supply of robots have increased at ProMat and within the industry over the last few years, having emerged from innovation hubs like Boston Dynamics and Massachusetts Institute of Technology (MIT), and that for supply chain challenges they can serve as a solution.
But he emphasized that these robots and their usage are not designed to downplay and downsize the human element and replace people but to augment their efforts and help them to be more efficient – at picking product primarily. Robots reduce travel, which is a human performance and productivity drain inside the distribution center, he clarified. “Workers can spend 60% of their day walking around instead of locating and picking product,” he said. “Fifty percent of all work in the warehouse is picking and 60% of that can be traveling.”
In fact, removing travel around the warehouse may be the single biggest cost that robots can remove, according to Kline. Imagine 300 to 400 pickers in a large warehouse walking around all day looking for products, he added. One way to cost justify investing in robots is to eliminate traveling versus automating picking.
Robots also eliminate “boring and repetitive” tasks, such as receiving and loading in the palletization area. “Tote-to-unit orders do not represent sought-after jobs,” he indicated. “Automating those tasks provides value and doesn’t require thinking. Companies want their people to focus on intellectual capital and thinking.”
The challenge, of course, is that companies need to be patient with ROI, according to Kline. “Integration costs can be high,” he noted. “Over time, robots can be faster and cheaper, but the first robot installed carries all the costs to start.” In short, robots represent high upfront costs that can deliver promised savings over time.
Kline also recognized the popularity of AI and machine learning and sought to clarify -if not distinguish – impressions of these options being panaceas. “They influence decisions more than solve problems,” he said. “We look at AI and machine learning as tools to solve problems.”
Bottom line: Experts generally agree that employing technology can offset labor/workforce challenges, but companies need the inventory volume to cost justify investing in and using what’s available and on display. They also acknowledge and stress that no one technology solution fits for all problems.
Among the considerations for cobot and robot adoption and implementation? Integration with internal systems – including inventory and warehouse management as well as with financial. How easily and quickly the technology can interface with an enterprise-resource planning (ERP) system. Plug-and-play within a day or two? How much weight can the cobots and robots handle? Are they equipped with digital mapping software to independently navigate through a facility? Are they equipped with sensor technology that enables them to avoid human and inorganic obstacles?
Otto Motors demonstrated its fleet whereby the largest model can move a 1,200-pound payload capacity. Through the Fleet Manager app, operators can regulate routes and speed limits individually and universally – customized and stratified according to operational needs.
Locus Robotics showcased its fleet of robots with the largest model capable of moving 600 pounds, and smaller models used for picking and sorting whereby five-to-six robots can be managed by a single human picker handling several thousand lines per day.
Unbox demonstrated its small unit designed to handle vertical sorting in compact spaces. Software enables floor and narrow aisle navigation with short vertical lift capabilities. Brightpick showed something on a bit bigger scale and even named their robots after popular characters from the “Star Wars” films.
The AGVs and AMRs themselves can be motorized flatbed platforms, multi-rack units with shelving towers and forklifts for moving pallets. AGVs and AMRs that don’t require humans to move product bins to and from rack or shelf employ mobile arms or slides to handle the tasks.
Avidbot demonstrated an AMR for scrubbing floors that is equipped with digital mapping and sensor technologies for autonomous operation but also enables humans to operate it in a manual setting. The company allowed attendees to take it for a test drive around the booth floor.
At least one AMR manufacturer – Thira Robotics – promoted its models as being able to navigate and move on damaged, uneven floors – when floor surfaces are not flat, smooth or even shiny, but include cracks, moisture/puddles, small debris, angled/skewed surfaces or ramps. But a Boston Dynamics executive across the hall countered with “we haven’t met a floor that our robots can’t drive on yet.” Boston Dynamics demonstrated its cobot model, but its robotic dog model drew big crowds.
Most of the mobile cobots and robots on display were on wheels, but Agility Robotics pushed the envelope of possibilities by showcasing robots with legs that resembled humanoids moving bins from a vertical storage unit to a conveyor belt.
View the video here of “Digit” the robot in action.
Notable cobot and robot companies:
- AddVerb (www.addverb.com)
- Agility Robotics (www.agilityrobotics.com)
- Avidbots (www.avidbots.com)
- BlueBotics (www.bluebotics.com)
- Boston Dynamics (www.bostondynamics.com)
- Brightpick (www.brightpick.ai)
- CoEvolution (www.coevolution.ai)
- Covariant (www.covariant.ai)
- Fanuc America (www.fanucamerica.com)
- Locus Robotics (www.locusrobotics.com)
- Otto Motors (www.ottomotors.com)
- SVT Robotics (www.svtrobotics.com)
- Seegrid (www.seegrid.com)
- SICK (www.sick.com/us/en/)
- Thira Robotics (www.thirarobotics.com)
- Tecsys (www.tecsys.com)
- Unbox Logistics (www.unboxrobotics.com)
- Universal Robots (www.universal-robots.com)
Forklift fancy
To a supply chain professional, a logistics and materials handling show without forklifts on display might seem like a vintage pharmacist with a mortar but missing a pestle.
Attendees traversing the ProMat show floor saw plenty of traditional forklifts on display as well as simulation technology to train forklift operators – some requiring virtual reality headgear to immerse participants in the experience while others allowed them to look around the booth to converse with friends.
Just as electric and hybrid cars have gained a popular foothold among consumers, however, more advanced forklift models running on battery power and festooned with cameras, computer screens and sensor arrays also attracted crowds.
If you’ve ever forklifts in a warehouse, you’ve probably noticed plenty of dents and scuff marks on the vehicle’s body where the forklift most likely collided with such things as aisle posts, racks and shelving units. Instead of promoting the battle-scarred, well-worn look as badges of heavy use and pinstripes of process, Hyster-Yale rolled out updated and upgraded models as part of a near “luxury logistics” category, opting to design and build these workhorse vehicles around their operators.
Hyster-Yale’s new forklift End Rider comes equipped with air suspension, ergonomic pads and hydraulic flooring on elongated beds to relieve foot, knee and leg pressure of the operators. Optical sensors check and watch operator feet movement to prevent injury. The forklift also includes adjustable controls that can be custom-fit for improved operator control and can be programmed at the touch of a button by operator experience and skill level. It sports a 30-degree slope of handle, LIDAR sensor-driven directionals along the bottom for scanning foot traffic and signaling. In fact, the LIDAR scanner searches out some 20 feet around the forklift, and if it spots an obstacle, it alerts the operator and automatically slows the forklift, similar to a car’s antilock braking and lane-assist systems. Powered by a lithium ion battery, it is 38% more fuel/energy efficient.
Through the system’s situational awareness sensors, the forklift helps to prevent tailgating and slows down at corners. It’s designed to help enforce positive behavior and helps newly trained operators by learning their centers of gravity and tracking what they do to prevent tipping as well.
Why the need for more advanced forklifts? Labor and workforce shortages, Hyster-Yale executives say. Companies are seeing 50% turnover in operators, so Yale wants to offset the cost to retrain new workers with this technology. In fact, through Yale’s Warehouse Academy, workers can be trained, certified and licensed even without prior experience. This Yale’s technology helps to prevent rack and shelving damage as well as injuries to workers, which reduces liability and lost time on the floor.
Another option for the next-generation forklifts on display involves autonomous operation, as shown by Third Wave Automation. The company’s high-reach autonomous forklifts also sport 3-D LIDAR sensors that scan for obstacles while in transit. Third Wave-equipped forklifts can be operated by a person directly or remotely and even be programmed for autonomous tasks. The software system includes safety measures that slow the vehicle when in transit, regardless of operation option.
Bastian, a Toyota Advanced Logistics Co., also demonstrated its autonomous forklift pallet mover.
Even as Third Wave executives promoted the forklift’s sensor capabilities they acknowledged a work-in-progress in that when a forklift enters a refrigerated area and returns to the warehouse floor the temperature change can create condensation on the sensor lens, which can affect detecting abilities.
They also noted that newer forklift models can traverse narrow aisles between high vertical shelving and perform storage and retrieval tasks by functioning as a “turret truck” with the ability to move the forks at a 90-degree angle to the left or right, such as Aisle Master. Big Joe demonstrated how warehouse workers can go vertical for manual picking of boxes and cases or inventory tracking.
Motion 2AI showcased its forklift tracking and wireless AGV and AMR software that emits real-time live streaming and location services to reinforce productivity and safety. SICK, a 75-year-old company, showed how its 360-degree LIDAR sensors with spinning lasers can detect anything moving around automated forklifts, AGVs, AMRs and even cobots and can automatically direct these vehicles to the proper pallet to pick up product.
Whether humorous or ironic, one of the exhibitors showcasing pallet proximity sensors was named HIT-NOT.
Notable companies:
- Aisle Master (www.aisle-master.com)
- Bastian (www.bastiansolutions.com)
- Big Joe Forklifts (www.bigjoeforklifts.com)
- Hyster-Yale (www.hyster-yale.com)
- Motion 2AI (www.motion2ai.com)
- SICK (www.sick.com/us/en/)
- Third Wave Automation (www.thirdwave.ai)
- Vecna Robotics (www.vecnarobotics.com)
Charged and in charge
AGVs, AMRs and most everything that runs on rechargeable batteries require time to charge, which takes the mobile devices and vehicles out of circulation and use. Historically, these vehicles move to their charging either attached to the floor, post or wall and plug themselves in.
At ProMat, Wiferion asked why tether? The company demonstrated its wireless power-charging technology that can be used by any product so long as the end user uploads the software and integrates with the charger. Empowered by Wiferion, the mobile product simply rolls itself over the floor-mounted charging plate or next to the wall-mounted charging plate.
Notable companies:
- Conductix-Wampler (www.conductix.us)
- Wiferion (www.wiferion.com/us)
SIMply irresistible options
ProMat attendees enjoyed some hands-on participation via heads-up displays as several exhibitors, such as Simlog, allowed them to try driving a forklift. Depending on the software product, operators could don VR goggles to complement the computer experience on oversized single screens or navigate their vehicle while watching three viewscreens.
Simulation software on display wasn’t limited to virtual forklift operations training. Other companies, such as Honeywell, Rockwell Automation and Siemens, demonstrated their 3-D software technologies to enable organizations to design and redesign warehouse footprint and layout for productivity gains and more efficient throughput as a key component of warehouse management.
Rockwell Automation acquired Emulate 3-D four years ago and incorporated their technology to help companies optimize processes through interactive multicolor layouts. Using machine learning, the software can adapt scenarios input by end users to show how processes and risks change when product volume doubles, for example, so that they can validate findings in a virtual environment before bringing it live and at scale.
The intralogistics division of Siemens also demonstrated its software simulation programming designed to optimize plant operations and performance. Siemens software creates a digital twin of a warehouse operation and enables end users to rearrange components and redesign the layout to track workflow. Either a team from Siemens works with clients onsite or clients can acquire the software via license and subscription to work virtually.
Notable companies:
- Rockwell Automation (www.rockwellautomation.com)
- Siemens (www.siemens.com/global/en/markets/intralogistics.html)
- Simlog (www.simlog.com)
Bearable wearables
Want to look like Disney/Marvel super-hero Iron Man without the perceived discomfort of wearing armor? Then get into logistics and materials handling to don wearable computers to communicate, track inventory and transact business.
Honeywell demonstrated how wrist and ring scanners – enabled through voice commands, if desired – can scan and show rows and stations to identify, locate, pick and restock products. Internally programmed maps via Android empower the end user to scan a bar code or speak information about a product so the wearable system can direct the end user precisely where to go.
ProGlove and Rufus Labs showcased similar wearable technology options for “hands-free” scanning. ProGlove also highlighted a pocket-worn recorder that tracks and transmits movement akin to supply chain steps for efficiency.
Several exhibitors promoted the concept of “vision picking” via computer-directed heads-up display as offering more effectiveness and efficiency, particularly when abbreviated training and onboarding due in part to labor challenges and staff turnover are necessary.
Lucas Systems promoted “Jennifer,” its speech recognition and voice-directed software for logistics and materials handling. Jennifer is designed to replace paper clipboards, tablets and wrist and ring computers. Jennifer, which paces and works at the speed of the person she is “directing,” actually predates Alexa and Siri. End users can adjust her voice as well as pick from 35 different pre-loaded languages so no translation software is needed.
Through artificial intelligence and machine learning, Jennifer directs the end user quickly and efficiently to the desired product wherever its location.
Wearable options weren’t limited to computer technology. Several exhibitors (Ottobock, HeroWear and Verve Motion) also stressed the ergonomic and safety benefits of wearing exosuits to reinforce joints, muscles and postures of workers lifting and moving boxes.
Ottobock showed Suit X, an all-mechanical exosuit for shoulder and back support. The suit incorporates a bungie cord and pulley system. The back support option includes nitro gas cylinders that function a bit like hydraulics. These suits work to transfer load lifting to the legs from the back so as to alleviate 50% of the pressure on back muscles and the spine.
Want to do your high-end, minimally invasive surgeons a solid? Ottobock also markets their exosuits to surgeons who perform complex, intricate, time-consuming, 10-hour operations to relieve fatigue and reinforce posture as these surgeons may be in a sitting position while working minimally invasive robotic controls.
HeroWear, which was spun out from the biomechanics laboratory at Vanderbilt a few years ago, also emphasized that its exosuit shouldn’t be limited to the warehouse. In fact, they work with Mayo Clinic and Vanderbilt and promote HeroWear for clinical and operational functions, including surgeons, and doctors and nurses for lifting patients, as well as for facilities management and maintenance staff for beds and stretchers. They launched their second-generation suit the week before ProMat.
Notable companies:
- HeroWear (www.herowearexo.com)
- Honeywell (www.honeywell.com)
- Lucas Systems (www.lucasware.com)
- ProGlove (www.proglove.com)
- Ottobock (www.suitx.com)
- Rufus Labs (www.getrufus.com)
- Verve Motion (www.vervemotion.com)
Taking the high road
Because hospital and warehouse space can be at a premium, organizations may find it difficult to expand storage facilities and have to contract with their distributors or third-party logistics companies for available space or alternative delivery frequencies.
But if they choose not to go out and about, they can choose to go up as well as narrow the aisles between racks and shelving. Plenty of exhibitors showcased towers of racks and shelving several stories high. To pick, stock and track products on these “ceilingscrapers” demonstrated automatic and manually directed hydraulic lifts as well as mobile robotic-manned “goods-to-person” cube storage automation units typically known as “AutoStore.”
AutoStore enables modular dense storage up to 16 bins high for light goods and is popular in electronics, grocery and retail environments. It hinges on a framework grid that supports battery-powered robots moving on X and Y axes. The robots maneuver based on orders received and are intelligent enough to know when to recharge. Products are stacked based on demand frequency. The smallest footprint may be about 1,000 square feet using 20 robots with 4,000 bins under 100 pounds of inventory per bin; the largest systems may use 500 robots accessing 100,000 bins.
What’s an alternative if logistics and material handling professionals don’t have AMRs or vertical lifts to reach those racks in the warehouse stratosphere for inventory counting, tracking or even picking? Drones may be an option.
Gather AI demonstrated how “autonomous inventory management” using drones equipped with machine-learning software can serve as eyes that can take photos and compare data to what’s on record within the warehouse management system. The drone can scan 15 times faster than traditional cycle counting and perform a real-time audit as well.
End users either fly the drone remotely around the warehouse taking photos to create a digital map as part of its real-time location capabilities or they program it to fly itself. The drone can offset labor shortages and add a bit of excitement to monotonous cycle counting. In fact, to retain its cycle counting team workforce, one Gather AI client actually rechristened the group the “drone research team.”
Tecsys also promoted the use of drones that can fly with a remote controller or autonomously without one and avoid obstacles – including oversized ceiling fans – as well as scan inventory on high racking or shelving inside the warehouse or out in the yard. Computer programming enables the drone to create photographic and videographic 3-D modeling of the warehouse interior and exterior for digital mapping and deployment. Pilots can be trained within half a day and the drone can be fully up and running in a day. Tecsys executives cautioned that the return-on-investment for drone use depends on frequency of use for cycle counting as well as unmoving product volume and ability to retain and maintain labor.
Notable companies:
- AutoStore (www.autostoresystem.com)
- GatherAI (www.gather.ai)
- Tecsys (www.tecsys.com)
Tote-ally essential
While cobots and robots may have their pros and cons, supporters and detractors, Flexcon (www.flexcontainer.com) urges logistics and materials handling professionals to look beyond the technology and additionally to the containers retrieved and transported.
Flexcon President and Product Manager Ken Beckerman (yes, he happily wears both titles to show leadership as well as product expertise), emphasized that amid the excitement of using cobots and robots, supply chain pros must have that technology work with the “right tote.” Why?
“The right tote makes automation work and work faster,” Beckerman told Healthcare Purchasing News. “Otherwise, robots have to do more work.”
Beckerman references how usage can cause tote walls to bend, bow brake or crack based on the weight of contained product or exposure to moisture. “It’s harder for robots to handle totes that bow out as the robot would have to calibrate,” he added.
Beckerman’s company showcased three kinds of totes in its booth – plastic, cardboard (resin) and high-density foam. Injection-molded plastic may give the perception of durability, he cautions, but it can crack.
The bulk (70%) of Flexcon’s tote manufacturing is customized for the client (including pantone-matching color, shape, size and logo imprints), according to Beckerman. The remainder (30%) are ordered through the company catalog. Flexcon also makes AutoStore dividers and walls as well as an extremely durable octagonal tote and one that can be water-logged – a fast-draining sprinkler tote that can withstand fire suppression when necessary.
Warehouse footprint, layout tips from industrial material handling experts
CHICAGO – To coincide with the May 2023 edition feature topic of storeroom and warehouse workflow in healthcare facilities, Healthcare Purchasing News traversed the exhibit hall show floor of the Material Handling Institute’s (MHI) ProMat conference and exhibition, asking non-healthcare executive experts for their insights on designing footprints and layouts – specifically, the biggest challenges faced in the process. Here’s what some shared.
“It goes without saying that planning is key to success in designing a new storeroom or warehouse. Most of the planning will consist in using historical data to help plan the future, unfortunately good data is often difficult to get as hospital organizations are limited by the use of basic material management functionalities from their ERP. My recommendation would be to use whatever data is available and try to get the most out of it for the initial set up. Ideally as you set up your new storeroom/warehouse you will be implementing more advanced tools that will support ongoing dynamic slotting allowing you to optimize as you move forward. In thinking through the workflows, you should re-consider existing ones based on optimal workflows supported by software technology such a Warehouse Management Solutions or Automation technologies such as ‘Goods to Person’ robots or others.”
Emmanuel Langlois, Executive Vice President, Generix Group
“Slotting for effective and efficient order picking. Remember the Golden Zone. Your fastest movers should be closest to dispensing to minimize travel. Slow movers should be placed in the back on shelves and high up or down low.”
Jim Hess, Director, Business Development, Warehouse Products, Hyster-Yale Group
“Space. Aisles need to be sized accordingly and linked to the technology installed. This includes the number of points from which to pick up stock to the distance needed to travel within a specified area – even to a different floor.”
David Friess, Channel Partner Account Manager – Global, Otto Motors
“The No. 1 sign that a project succeeded: A person on the customer side needs to be engaged and passionate and have a very clear vision of what you want to accomplish and do. You may know what you want to do you but don’t necessarily have be to be sold on a solution. You have a clear vision and work through the problems. Start with a pilot that is easy to conceptualize. Get people comfortable with their roles. People are more important than machinery. They are what makes your business run.”
Adrian Ennis, Technical Marketing Manager, Otto Motors
“The biggest challenge in hospital systems is slotting. It’s less about layout than about placement of products. Where do I put what items and why? Like a closet with stuff thrown around. Stuff you use more often should be close and near the front. Other stuff can be up high and far back. Consistently look at demand profiles and locations. It’s more about where stuff is located in the warehouse. That problem is a moving target due to seasonality, promotions and sales. It depends on labor, too. You’ll need more if you’re unorganized. Lots of companies do re-slotting twice a year. The best way is to employ dynamic location slotting where you move stuff on a regular basis. It’s a neat way to change the game as a person or two runs models to determine [a solution.] Everything has to be about delivery now to be top-notch in distribution. Retailing is all about real-time warehousing. A lot of it hinges on software. You can put in conveyors but need to determine the best cases. If you put in robots, now what? You have to have a plan. These robots are not self-aware.”
Ken Ramoutar, CMO, Lucas Systems
“[It’s] good to have planning software ahead of time to map out what you want to do.”
Ryan Diehl, Solutions Consultant, Siemens Digital Industries Software
“When you buy a vertical carousel, you need the right totes to place on or within them. You have to have the right totes for vertical carousels.”
Ken Beckerman, President and Product Manager, Flexcon
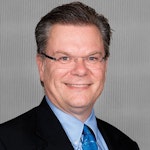
Rick Dana Barlow | Senior Editor
Rick Dana Barlow is Senior Editor for Healthcare Purchasing News, an Endeavor Business Media publication. He can be reached at [email protected].