Submit your questions
email: editor@hpnonline.com
phone: (941) 927-9345 ext. 202
Q I attended a CS workshop recently, and one of the sessions was focused on the various functions in the reprocessing of medical devices and the need for monitoring and quality assurance. The speaker was very good although vague on some of the specifics of the actual monitoring processes. She also discussed the various tools and methods that are available to implement a good QA program for cleaning and sterilization. However, in her presentation she implied that it was a requirement to maintain documentation on the seal integrity and the performance of heat sealers used for sealing peel pouches, but she was not able to provide a reference source or advise on how that could be done. Since the workshop, I have looked through the various standards – AAMI, AORN and the like – but have not been able to find any such recommendations, nor have I been able to find any products or tools for monitoring the seal integrity. Any information you might be able to share on this matter would be appreciated.
A The speaker perhaps was thinking about the ISO standard which states that there should be a documented process validation program demonstrating the efficacy and reproducibility of all sterilization and packaging processes. The sterile barrier system manufacturing process, including the sealing of sterile barrier systems shall be validated. The validation shall include at a minimum, an installation qualification, an operational qualification and a performance qualification at this order. Operational qualification (OQ) in the sealing process is to obtain and document evidence that the sealer operates within predetermined limits when used in accordance with its operational procedures. The critical sealing parameters in this regard are temperature, time and pressure. These parameters have to be adjusted as per the packaging material sealed.
Some time ago AAMI published a TIR guidance document which complimented the ISO standard. The rationale here is that you want assurance that your heat sealer does indeed perform properly and consistently. It of course is important to ensure that the appropriate temperatures, pressure and time are reached to adequately seal the type of packaging you are utilizing. As you know there are different materials used in the manufacturing of peel pouches i.e. paper, polymers, plastics, Tyvek etc. Each type of material may require a very specific temperature and time to ensure proper sealing without damaging the packaging material. Peel pouches differ from manufacturer to manufacturer, so it is critical that you obtain and follow the specific instructions from your packaging manufacturer. The instructions should provide all of the required parameters for sealing your peel pouches. The Sterile processing department should incorporate an OQ (Operational Qualification) process into their sterile packaging quality assurance policies. The OQ should provide verification of the heat sealer’s ability to consistently provide an appropriate seal closure to ensure the sterile integrity of package contents.
There are commercial QA products available on the market which will allow you to monitor, test, verify and document the quality performance of your heat sealer on a daily basis. (See Figures 1 and 2).
The device is designed for operational qualification of the sealing process efficacy. In the sealing process the following quality properties of the seal can be monitored and controlled:
- intact seal for a specified package seal width
- channels and open seals
- punctures or tears
- material delimitation or separation
- On each Seal Control device the following documentation is maintained:
- date and time of test
- sealer identification
- sealing parameters
- control authorization
- test results
- corrective actions/adjustments to sealing parameters
- special notes/comments
- maintenance information
- authorized signature
The sheet paper of the Seal Control device is preprinted with a marking area for the aforementioned documentation and any corrective actions required or taken. A visual inspection of the Seal Control sheet must be conducted. The colored film of the sheet turns to a darker shade of green in the sealed areas, thus providing a valid visual assessment of the quality of the seal. The pre-sealed edges of the sheet are a reference for the darker shade of color. In the event that the test results are unsatisfactory the test has to be repeated. If the test results are satisfactory, the sheet is signed by an authorized person and kept on file with QA records. Faulty heat sealers should not be used until serviced and their satisfactory performance can be verified with the Seal control QA device.
About the Author
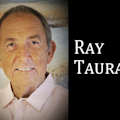
Ray Taurasi
Ray Taurasi is Principal, Healthcare CS Solutions. His healthcare career spans over five decades as an Administrator, Educator, Technologist and Consultant. He is a member of AORN, SGNA, AAMI and a past president of IAHCSMM. Taurasi has been a faculty member of numerous colleges teaching in the divisions of business administration, nursing, and health sciences. He is the author of numerous articles and textbook chapters; he is a frequent speaker at national and international healthcare conferences.
Note to readers from Ray Taurasi - In 2021, my life’s career path will transition to one of new opportunities and adventures. As a result, after nearly 19 years and 225 CS Solution columns, this edition will be my last.
“All changes, even the most longed for, have their melancholy; for what we leave behind us is a part of ourselves; we must die to one life before we can enter another.”– Anatole France
I wish you and your loved ones a healthy and joyful holiday season and a beautiful New Year! God Speed, Ray
https://www.facebook.com/pages/category/ Local-Business/Healthcare-CS-Solutions-128857 3061153887/ • email: raytaurasi@gmail.com