Q
“We have an eyewash station in my department. What are the standards that we should be following to make sure they are safe to use anytime? In fact, the eye cover is off the eye shower, and the tag attached is not filled out. What should I do?”
A
When it comes to emergency eyewash stations, there are plumbed and non-plumbed types (Fig. 1). This article will focus upon plumbed emergency eyewash stations. In my view, the type that should be in a medical device reprocessing department is a plumbed emergency eyewash station because it allows the person to use it hands-free once actuated.
When it comes to ensuring staff safety for using plumbed emergency eyewash stations, ANSI/ISEA Z358.1-2014 standard is what is referenced worldwide.
Within the United States, it is a combination of documents a) OSHA , b) ANSI/ISEA Z358.1-2014, and c) ANSI/AAMI ST79 (and ST90) that govern eye wash stations. The latter of which takes its reference from OSHA for its standard.
“The decontamination area must have an emergency eyewash/shower station…eyewash stations should not be in a location that requires flushing of the eyes in a decontamination sink.”,
Medical facilities with departments that reprocess medical devices utilize chemicals that employees can be exposed to; thus, they need to provide plumbed emergency eye stations in case the employee gets any chemical(s) in their eyes, and they must flush their eyes.
“If eye contact with a chemical or contaminant occurs, the eyes should be immediately flushed with large amounts of water according to the SDS.”
To ensure that a plumbed emergency eyewash station is performing properly, ANSI/ISEA Z358.1-2014 outlines what needs to be tested weekly to help ensure safety of the staff that these pieces of safety equipment are working when needed.
· Verify flushing fluid supply at the delivery head of the device.
· Clear supply line of any sediment buildup potentially preventing fluid delivery.
· Minimize microbial contamination because of standing water.
Document the a) date, b) person testing, c) location of the plumbed emergency eyewash station, and d) the temperature, according to your facility’s policy on record retention.
“Properly maintained eyewash facilities”
The presence of emergency equipment is not meaningful if the equipment is not maintained in working condition. Thus, for the plumbed emergency eyewash station a Quality Management System approach is needed to ensure it is working properly (IQ, OQ, PQ).
ANSI/ISEA Z358.1-2014 requires eye and eye/face nozzles to be protected from airborne contaminants and full bowl dust covers provide additional protection from debris/trash accumulating within the eyewash bowl. This should be noted upon actuation the eye covers operate properly.
Based upon medical recommendations and various physiological studies, the ANSI/ISEA Z358.1-2014 standard requires that tepid (temperature range is 60- to 100 °F [16- to 38 °C]) flushing fluid be delivered. This temperature should be kept for at least one-minute after actuation of the eyewash station.
The information presented in the article is taken from ANSI/ISEA Z358.1-2014, which covers all types of emergency showers, eyewashes, eye/face washes, and combination units. The standard is intended to provide uniform, minimum guidelines for their performance, use, installation, test procedures, maintenance, and training.
Once again, the information here has focused on the plumbed emergency eyewash station because this is the recommended type of emergency eyewash station (most used) for staff who work within a medical device reprocessing department.,
Broken eyewash cover
In my view, regardless of who is responsible for checking the plumbed emergency eyewash station, it is still the management of your department that is always accountable for the station being in working condition. That is why I always suggest the department should own the testing process.
References
1. Baugh, L. (2015, August 27). Free User Guide Helps Ensure Proper Use, Selection of Emergency Eyewash, Shower. ISEA. https://safetyequipment.org/knowledge-center-items/free-user-guide-helps-ensure-proper-use-selection-of-emergency-eyewash-shower/. (URL shortened: https://is.gd/xvZqKf).
2. Occupational Safety & Health Administration (OSHA). (1982, March 8). 29 CFR 1910.151(c)-Medical Services and First Aid. United States Department of Labor. https://www.osha.gov/enforcement/directives/std-01-08-002.
3. AAMI. (2017). ANSI/AAMI ST79:2017 Comprehensive guide to steam sterilization and sterility assurance in health care facilities [3.3.7]. Association for the Advancement of Medical Instrumentation (AAMI).
4. CSA Group. (2018). CSA Z314.18 Canadian medical device reprocessing [6.7.2.3]. Canadian Standards Association (CSA Group).
5. CSA Group. (2018). CSA Z314.18 Canadian medical device reprocessing [6.7.2.3]. Canadian Standards Association (CSA Group).
6. CSA Group. (2018). CSA Z314.18 Canadian medical device reprocessing [10.2.2.1.2(g); 12.2.1(h); 13.2.2; Table F1]. Canadian Standards Association (CSA Group).
7. AAMI. (2017). ANSI/AAMI ST79:2017 Comprehensive guide to steam sterilization and sterility assurance in health care facilities [3.3.7]. Association for the Advancement of Medical Instrumentation (AAMI).
8. Kelechava, B. (2014, July 3). ANSI/[ISEA] Z358.1-2014: Emergency Eyewash & Shower Standard. American National Standards Institute (ANSI). https://blog.ansi.org/2018/07/emergency-eyewash-station-shower-ansi-z358-1/?unapproved=27892&moderation-hash=a37b21ce0b9db93421b1774ec4f6c1aa#comment-27892. (URL shortened: https://is.gd/JoorjB).
About the Author
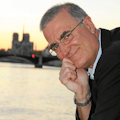
Stephen M. Kovach
Stephen M Kovach, BS, CFER, started in the medical field in 1975 as a sterilization orderly and has worked in many positions within the Healthcare Industry. He presently is Clinical Educator Emeritus at Healthmark, A Getinge company.