Those who have experienced one or more surveys from The Joint Commission (TJC) should have a relatively good idea of what to expect for future surveys. Yet, Sterile Processing (SP) professionals across the country are often surprised when a survey is on the near horizon, and even more surprised when they receive citations from surveyors. Ideally, seasoned SP leaders and technicians would work proactively to identify issues within their responsibility and fix any outstanding issues long before a survey occurs.
Preparing for a TJC survey should be part of daily practice and not just in the days or hours before surveyors arrive. As a consultant who assesses dozens of hospitals each year, however, it is discouraging to see how unprepared many SP teams are. It is important that SP leaders and their teams understand that deficiency findings identified by TJC surveyors may trigger a subsequent survey from the federal Centers for Medicare and Medicaid Services (CMS). If this happens, CMS will not only survey the SPD, but the entire facility as well. These steps can help SP professionals prepare for upcoming surveys:
Review the past. It is rare that TJC surveyors will appear unannounced unless an organization has had issues in the past or a serious negative patient event. Therefore, SP leaders typically will have ample time to devise a survey preparedness plan. Start with a review of previous TJC surveys to review what recommendations or findings were given. Understanding previous performance will help leaders and staff better prepare for the upcoming survey.
Conduct mock surveys. Mock surveys help all employees better understand the survey process and what to expect. The more trial runs are performed, the more comfortable employees will become when they are questioned by a surveyor. (Note: Surveyors seem to have a knack for picking out the newest employees, so ensure everyone is prepared.)
Review policies. It is prudent to carefully review the department’s policies and procedures to ensure they align with current standards and best practices.
Get back to basics. Infection prevention practices, standards, regulatory guidelines, and instructions for use (IFU) are the blueprints for setting up and maintaining a well-run SPD. Understanding SP-related challenges and the various practices that go into maintaining a highly functional department is critical for managing day-to-day operations. If a leader cannot keep their department clean, well-organized, and maintained, it will become especially difficult to manage the larger, more complex aspects of the job—an outcome that will surely be noticed by surveyors.
Prioritize education, training, and communication. SP leaders should consider the following:
· Are staff members fully trained in all areas of SP operations?
· What is the process to orient new employees?
· Can all employees answer basic survey questions?
· Have initial and annual competencies been conducted, documented, and included in employee files?
· Are regularly scheduled inservices provided, and is attendance documented?
Keep the department clean and orderly. Not only is maintaining a clean and organized SPD good for safety and positive outcomes, but it also sets a positive first impression during a survey. If the department is dirty or unkempt, the surveyor may wonder what else is falling short. Each area (decontamination, assembly, sterilization, and storage) should be routinely cleaned and free from dust and debris. Workstations should be well-organized, functional (well-stocked), and cleaned regularly (each shift daily, weekly, and as needed), and computer stations should be cleaned routinely and organized (including wire management). Shelving and storage should be cleaned routinely and documented each time it is performed. Bottom shelving should have a solid surface and be elevated off the floor to allow proper cleaning. Tape, adhesives, and other sticky residue should be removed from all surfaces. This is essential because if hospital-approved cleaning products cannot contact the surfaces being cleaned, the device will be considered contaminated.
Repair and maintenance (work orders). Proper departmental maintenance is vital for safe, successful operations. For things the SPD cannot maintain or repair on its own, it will be necessary to place appropriate work-order requests. Such examples include patching and painting walls, replacing stained, broken, or missing ceiling tiles or damaged floor surfaces, and other equipment or structural damage. Temperature and humidity are other essential factors to maintain in the SPD. Surveyors may ask who is responsible for maintaining temperature and humidity logs, and inquire about processes taken when temperature and humidity fall out of an acceptable range.
Routinely monitor equipment. Monitoring of each piece of processing equipment should be performed to ensure the units are functioning properly. Sterilizer monitoring should be performed for each type of sterilizer in use and includes the use of challenge devices such as biological indicators (BIs) and chemical indicators (CIs). A surveyor will review this process, the frequency it’s performed, and whether the findings are documented.
Leverage technology and ensure standards and policy compliance. Are you able to trace an instrument, set, or endoscope from its origin to patient use and back to inventory? Do you have the most current standards, regulations, IFUs, and policies in a dedicated location that is readily accessible to all employees? Surveyors will ensure current practices align with best practices and the SPD’s internal policies and procedures.
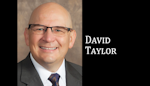
David Taylor | Principal, Resolute Advisory Group LLC
David L. Taylor, MSN, RN, CNOR is an independent hospital and ambulatory surgery center consultant and the principal of Resolute Advisory Group LLC, in San Antonio, Texas.