Enhancing your structure, structuring your enhancements
Upgrading the OR — or starting one from the ground up — requires more than the purchase and installation of booms, imaging equipment, robotics, surgical tables and other big-ticket items. Surgical suite planners will also need to consider the walls, floors, storage systems, scheduling technology, interconnectivity channels, temperature/electrical systems, and other items that are required to complete the project.
Start off on sure footing
Soraci says floor surfaces in the healthcare environment should be extremely dense so they can repel dirt naturally and also have minimal seaming and floor welds to ward off contamination, which are some of the features of nora floors.
“nora flooring can also mitigate risk in the OR by providing its staff with a safe and comfortable working environment; its non-coated surface helps reduce slips, trips and falls,” said Soraci. “nora flooring can reduce musculoskeletal injuries and physical fatigue from prolonged standing during a surgical procedure. In addition, this flooring system does not chip from dropped objects and is designed to withstand intense point loading and extreme rolling loads, making it an ideal application for surgical suites.”
Cleaning is a breeze as well, she added. “nora’s flooring requires little more than water to clean resulting in improved indoor air quality (IAQ) by eliminating exposure to cleaning chemicals. In addition, nora premium rubber has a no-wax protocol, which translates into a lower outlay for maintenance and increased uptime in the OR.”
“Once a person enters the room, the room is potentially contaminated by the microorganisms that are on the bottom of their shoes,” said Scott Beal, Chief Operating Officer, at Green Earth Medical Solutions (GEMS). But if those shoes are disinfected before walking through the OR door, they become far less contaminated. The PathO3Gen Footwear Sanitizing Station (FSS) from GEMs provides a solution. “Step on the station, wait 6 seconds as the UVC and Ozone penetrates and destroys 99.9 percent of the capsid/outer wall and DNA of deadly pathogens on the bottom of your shoes. The germs are destroyed, then step off and go,” Beal explained. The device can also be used throughout the facility to thwart contamination.
Surgical suite space is precious
When building or retrofitting the OR, every square inch matters. “The space within the four walls can only handle a certain amount of equipment, people, and inventory necessary to perform a successful procedure,” stressed Ian Loper, Vice President, DSI Direct. “OR departments and their Central Core and OR suites have always struggled to adapt to the operating theatre’s workflow, space limitations, configurability of the equipment inside the room, and adjustability of the storage equipment for just-in-time retrieval of supplies.”
When it comes to OR cabinetry/storage, there are several factors to consider. Outside of space configurations and convenience, Loper says modern storage systems for the surgical suite should offer features specifically designed to benefit both clinicians and patients.
“With value stream analysis all the rage in healthcare right now, the expected outcomes are to eliminate stock outs, eliminate expired supplies in stock, enhance visual indicators for quickly identifying supplies, and becoming LEAN in all facets of the daily operation,” said Loper. “Between renovations and new construction projects across the country, we’ve noticed a movement towards high-density stainless steel storage systems with an integrated accessory package for a range of supplies, catheters, stints, peel packs, and blue wraps within one standardized unit in the suite to maximize the valuable footprint. We’ve also seen a trend for allocating a dedicated mobile exchange/transport cart for specific services and procedures that can be rolled from one room to another. The objective is to never leave the room during a procedure to go pull supplies which could lead to unwarranted delays.”
In addition to enhancing access, productivity, ergonomics, and inventory management processes, the custom-configured DSI Modu-Cab and Modu-Cell systems satisfy critical standards related to sterility compliance and other safety measures — features that ultimately help surgical staff to deliver the best possible care to their patients.
Utilization escalation
To give an example, Harber explained how one hospital approached anticipated growth while still maintaining key performance indicators around OR cost and utilization after it partnered with a large insurer.
“The hospital found that by localizing equipment and supplies by specialty, it could improve workflow and dramatically decrease turnover time; this change, however, would require the hospital to completely change its approach to allocating OR time, including coordinating surgeon and staff scheduling to align with new block time,” Harber said. “To ensure a smooth rollout, the hospital used an operations management software platform from Hospital IQ to better understand the impact of consolidating service lines by location, as well as the specific block time demands of individual service lines. By aggregating the multiple data sources, the platform provided the system-wide visibility and block management capabilities to enable OR managers to allocate and measure the key performance indicators that they were looking to improve.
“Analytics gave this hospital’s leaders the insight they needed to understand how the changes to their OR suites can and should be optimized to meet key performance objectives and the time required to align resources and staff to patient demand,” he continued. “The hospital has decreased turn around time between cases. Block utilization has increased by around five percent, and the hospital has identified a number of opportunities for improvement and growth.”
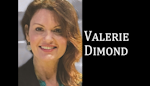
Valerie J. Dimond | Managing Editor
Valerie J. Dimond was previously Managing Editor of Healthcare Purchasing News.