The letter “e” — prefix to something or not — tends to align itself with anything related to finance, information technology, strategic planning or sustainability.
In Supply Chain, it stereotypically tends to represent “expense” — or to clinicians disgruntled when they can’t find what they need, “empty,” as in supply shelves.
The Supply Chain team at West Reading, PA-based Tower Health, eludes that designation.
To this august group of professionals, “e” stands for “enterprising,” which loosely translated signifies the freedom to be entrepreneurial within the confines of an established corporate structure.
Some healthcare organizations try to be forward-thinking and future-minded by outsourcing trouble spots to third-party consultants and vendors, or throwing some new automation and software at a challenge and hoping something clicks or sticks.
Not Tower Health.
Five years ago, the Reading (PA) Health System, comprising a 700-bed hospital and other healthcare facilities, operated like many other similar organizations. Since then, Reading has morphed into the six-hospital Tower Health with 116 healthcare facilities in its stable, fortified by a centralized corporate supply chain department that has posted some eyebrow-arching results.
To wit: All processes are electronic and automated, enabling transparent reporting and accountability, according to Rita White, Tower Health’s Vice President of Supply Chain. Product ordering and replenishment has been streamlined, resulting in a 60 percent improvement in inventory accuracy with an 80 percent reduction in stockout occurrences. Supply Chain sources and manages all Operating Room, Cardiovascular and other key area supplies, freeing clinical staff members to devote themselves to providing patient care.
Tower Health debuted formally and officially in October 2017, booking in excess of $27 million in costs savings to date. Today, Supply Chain is embedded into all areas of Tower Health and is an integral part of the patient experience, White emphasized, acknowledging that the transformation did not happen overnight. “It required intense strategic planning, a thorough understanding of organizational goals, and an innovative vision for how Supply Chain can support high-quality patient care,” she noted.
For investing in its own ingenuity, its own people and its own technology, Healthcare Purchasing News selected the Tower Health Supply Chain team as its 2019 Supply Chain Department of the Year.
Recharting the nucleus
Countering any chicken-and-egg relationship, White emphasized that Supply Chain’s metamorphosing changes weren’t related to Tower Health’s emergence and growth.
“Rather, they were reflective of new Supply Chain leadership that brought a new vision for the role of the department,” she indicated. “There was no ‘cause-and-effect’ between the growth of Tower Health and the implementation of the new initiatives. In alignment with the strategic approach of Tower Health, Supply Chain wanted to build solutions that would grow with the health system. If anything, she added, they were running parallel courses.
The Reading-Tower Health Supply Chain caterpillar-to-butterfly transformation started with the team itself as leadership sought to identify “required skill sets beyond traditional Supply Chain experience.” This included requirements that applicants achieve minimum scores on advanced technological assessments even to qualify for an interview. They also needed to demonstrate “innovative mentality, problem-solving abilities, analytical mindsets, project management skills and professionalism,” along with collectively displaying some proficiency in more than 20 different software programs and LEAN Six Sigma principles.
“We deliberately recruited talent with analytical skills, leading to a combination of logical thinking, technical know-how and professional work ethics,” White said. “Supply Chain leadership taught the team pertinent Supply Chain operations, communicated and clarified the ‘ask’ and vision of the initiative, and routinely monitored progress to ensure the solution was ‘staying on course.’ This empowered our team to develop ‘home-grown’ solutions specific to the needs of Tower Health and mine the data to obtain meaningful, informative insights.”
White quickly points out that their efforts do not diminish, but enhance traditional supply chain functions.
“Every time Supply Chain had an FTE opening, we enhanced our staff with additional skill sets, capable of developing, implementing, and maintaining Supply Chain operations based on prioritization,” she said. “By replacing time-intensive, erroneous, manual processes with automated, sophisticated solutions, we were able to enhance the roles of Supply Chain without compromising core functions.
“Healthcare as an industry is changing at an unprecedented rate with enhancements in technology, discovery of new treatments and evolving patient care,” White continued. “To proactively address exceptions, beginning with forecasting throughout the continuum of care, Supply Chain requires continuous access to real-time data from various systems, both internal and external. Traditional MMIS systems do not inclusively address all aspects required of a robust, well-rounded Supply Chain department. Our solutions close the gap between where the ERP system leaves off and the business needs.”
Such a multi-faceted team transcended the traditional Supply Chain silo mentality or even the next-level “multi-disciplinary” definition. The C-suite recognized this, too, actively encouraging any and all ideas, keeping a universal “open-door” policy in place and implementing support-area focused seating that paired groups of team members with different titles and responsibilities together in support of common areas.
“Clinical staff holds daily huddles to discuss patient concerns,” White noted. “While considering this, we discussed the type of advancements that could be made if all the positions supporting an area were seated together, enabling them to continuously brainstorm and strategize while enhancing communication between different supporting roles. This strategy promotes the ability of Supply Chain to provide comprehensive, consistent support to all areas.”
Power in data
Tower Health’s Supply Chain team recognizes and understands the value of data — from desiring it to collecting it to analyzing it to disseminating it. That’s why they operate under the ideology that “whoever holds the data holds the truth,” which they weave throughout their operations, spanning contract negotiations with vendors, performing supply-cost-per-case analyses on OR procedures, or determining ideal PAR levels to minimize waste. Detailed analytics fortify strategic decision-making.
“Supply Chain has a continuous commitment to maintaining data integrity, utilizing [internal] tools to monitor and resolve data exceptions as they occur,” said Ann Paolini, System Director, Supply Chain Business Intelligence. “To ensure the integrity of our data, only a select group of individuals have the security level required to modify the item master. Additionally, any data changes must go through standard, automated workflow processes to obtain approval.”
Tower Health’s Corporate Supply Chain was formed largely by the need to standardize operations at all facilities and integrate member hospitals under a single enterprise resource planning system, according to Paolini. Tower Health’s ERP from Infor integrates human resources, payroll, procurement, finance and accounts payable. Supply Chain’s item master interfaces with Epic for both patient documentation and billing. Tower Health also incorporates GS1 supply data standards, such as the GTINs, via the Food and Drug Administration’s Global UDI Database site.
Supply Chain also earned the respect and trust of the C-suite, according to Mark McNash, Senior Vice President, Support Services. (See sidebar on Tower Health innovations.)
“By replacing manual processes with an automated, standardized workflow, leadership requires only a simple internet connection to be aware of all pertinent information throughout the capital process,” he said.
Harmonic convergence
Before Tower Health could unwrap its unified brand identity in October 2017, the six systems had to jump through a few hoops. In the new era the corporate supply chain office would oversee product ordering, contract management and negotiations, strategic decision-making; and process management; local inventory functions, such as receiving, PAR replenishment and management of facility inventory levels would be handled by the facility’s Supply Chain team.
With that point of reference they needed to consolidate key suppliers and IT horsepower.
“The data [were] reviewed over a six-month period to create a single item master, which did not come without its challenges,” she recalled. “The acquired hospitals’ data had never been data-cleansed and was missing various item attributes. Now that we have integrated into a single ERP system, processes are being implemented to ensure a continual cycle of validating and cleansing.”
Plus, the item master conversion needed to predate the future rollout of their electronic health record and OR system from Epic as they wanted to plug the item master into it easily and seamlessly.
The consolidated item master challenge? They wanted to combine six independent, autonomous item masters — in a single day. And they did it.
“The ERP integration of the six Tower Health hospitals was a prerequisite for our Epic go-live this August,” said Michelle Trupp, Senior Vice President and CIO. “The health system agreed to an ambitious big-bang approach — all hospitals went live on our ERP system the same day. Incorporating and cleansing data from five new hospitals was a phenomenal task that no individual or department could manage alone. The collaborative efforts of IT and Supply Chain placed the foundation for a seamless and successful transition.”
White indicated that Supply Chain and IT currently are discussing future project development together.
To assist the blossoming and burgeoning Supply Chain team’s transition, departmental leadership created in Microsoft OneNote a comprehensive 300-plus-page manual that detailed all department activities.
“Supply Chain involves many moving parts, requiring complex processes and effective utilization of resources,” White noted. “Thorough documentation coupled with comprehensive training is often the most effective and rapid way to onboard new employees and train current ones on new processes and tools.”
They selected Microsoft OneNote as “the main documentation platform because it is an easily accessible tool that is available as part of most Microsoft Office packages and supported by IT,” White said. “This allowed the manual to be readily available to all team members, beginning at onboarding, which made it ideal for providing new team members with training materials. OneNote easily allows multiple people to view and update its contents simultaneously and offers a versatile home for a variety of training documents.”
Clinical progression
Like many supply chain departments, Tower Health’s team recognizes and understands the value of fulfilling its mission to clinicians, its primary customer base.
“We listened to the needs of the clinicians, determined the best ways to provide them with the needed support with a strong focus on being proactive instead of reactive, and consistently strove to go above and beyond the expectation,” White acknowledged.
To support Tower Health’s physician community, Supply Chain “reinvented” value analysis with its iVAT program. Why the lower-case “i?” iVAT includes the innovative design of interconnected sources to establish the integration of data resources into intelligent, analytical tools to drive informed decision-making to promote high-quality patient care, improved operations and positive financial outcomes, according to White.
Here’s how it works, according to White. iVAT is a corporate program with representation from each facility, incorporating Skype meetings to ensure maximum participation across all locations. A steering committee comprising executive leadership provides oversight to the program and ensures alignment with the strategic priorities of Tower Health. Because Tower Health doesn’t operate any local Value Analysis committees independent decisions are not made at individual facilities. To bridge the gap between corporate and local departments, Supply Chain dashboards leverage Tower Health’s intranet, which is available to all facility locations. To ensure easy access to tools at all facilities, Supply Chain developed a user-friendly, easy-to-navigate intranet site that forms a centralized portal and provides a single-point of access for all Supply Chain tools and team rooms via a dashboard.
“By working collaboratively to assess and coordinate our procurement activity at the system-level, the iVAT program impacts and benefits every associate and patient at Tower Health,” McNash said.
For each initiative, Supply Chain provides members of the iVAT collaboratives a detailed report called a “Prospectus,” which includes a summary of the data, including total financial impact, market share, key stakeholders and proposed item conversions to the SKU level across the Tower Health enterprise, according to White.
“Physicians respond to data, and the analysis of clinical financial data is integral to the collaboration of key stakeholders in improving patient care and identify savings opportunities,” said Gregory Sorensen, M.D., Executive Vice President and Chief Medical Officer. “iVAT utilizes an automated infrastructure to pull information from multiple sources, including Epic and [Infor] and structure it into meaningful, standardized information, promoting strategic decision-making.”
Shared services
Tower Health was one of five founding member health systems that formed a regional group purchasing organization called AllSpire that works with HealthTrust as its national GPO.
“This project has significant importance to Tower Health, not only because of the adverse impact ‘unknown spend’ has in accurately identifying cost saving opportunities, but also because of the need to support our integration efforts to bring six hospitals together into a consolidated ERP system and a single unified Item Master,” Paolini said. “Throughout ERP integration, we were in a period where we did not have visibility into the data of the acquired hospitals except through HealthTrust data feeds. We were reliant upon HealthTrust data to begin the integration process until all hospitals operated on a single ERP system.”
To date, the project has reconciled approximately $30 million of unidentified spending, she added.
Tower Health Supply Chain demonstrates innovative incubator from A to Q
When it comes to maintaining the delicate balance between creating and developing their own processes and technologies and outsourcing to a vendor, Tower Health’s Supply Chain team embraces a simple philosophy.
“Before developing an internal solution, Supply Chain always checks what is available on the market, so we don’t reinvent the wheel,” Rita White, Vice President, Supply Chain, told Healthcare Purchasing News. “Additionally, we attempt to partner with vendors who offer partial solutions – assuming the partial solution is cost-effective and not easy to replicate – with the opportunity to enhance their software and use us as a beta test. Only after exhausting these options do we resort to customization to address the business need.
“Supply Chain develops in-house solutions when we are unable to locate a third-party tool that is able to implement the kind of robust solution we require to fulfill our business needs,” she continued. “Supply Chain develops solutions that thoroughly address our needs instead of trying to limit our needs to fit the available solutions.”
Here’s a breakdown of what Tower Health Supply Chain uses to prevent breakdowns.
Aegis
During and after a crisis or disaster is when healthcare services are needed most – particularly for the influx of patients and the support systems that buttress the clinicians delivering those services.
Typically for Supply Chain, the enterprise resource planning system going down represents a recipe for crisis and disaster. Tower Health’s Supply Chain team, however, devised a tool to cover such a possibility. Aegis replaces the fundamental functions of the ERP system with an automated “Disaster Recovery Engine” that automatically generates storeroom picklists and vendor purchase orders without requiring the ERP system.
“During an ERP disaster, Aegis generates unique PO numbers that differ in appearance from an ERP auto-generated PO number,” said Ann Paolini, System Director, Supply Chain Business Intelligence. “These PO numbers are automatically stored in a separate file by Aegis and can be referenced at any time by Supply Chain staff. POs generated during disaster are not uploaded into ERP system. Payment is made within the ERP system with the Aegis PO instead of an ERP-generated PO.”
Meanwhile, PAR locations are counted as usual, but required product is noted manually, as the handhelds would be offline, too. These notations are then sent to the Supply Chain office, where all available team members use Aegis to enter the required product for each PAR. After entering the amount of product needed to replenish a PAR, team members need only click the buttons on the Aegis homepage to generate picklists and purchase orders.
Aegis automatically separates items that can be replenished from the storeroom from those that must be ordered through the vendor and places the product on a picklist or purchase order as appropriate. Further, picklists are automatically formatted and are designed to assist pickers with locating the needed product in the Storeroom as quickly as possible.
During the functional development of Aegis, Tower Health Supply Chain team consulted with their primary vendors to review the PO materials to ensure proper communication and processing.
Supply Chain remains prepared with Aegis as it rigorously has tested it and trained all team members on its use, but so far has not needed to activate it in a real-world scenario.
“Thankfully, we have not yet been faced with a situation where Aegis has been used, but Supply Chain has held ‘mock disasters’ to train team members on its use, which included our primary vendor, Medline,” Paolini said.
Automated expiration checks
for more accurate monitoring and tracking of product expiration dates, Supply Chain formally clipped the clipboard and converted to handheld terminals that transfer useful data to the ERP system, making field audits that much more efficient. In fact, White’s team’s efforts earned Tower Health a spot among the Elite 11 of HPN’s 2018 listing of Supply Chain Operations to Watch. (See December 2018 HPN.)
Previously, Supply Chain conducted expiration audits manually. In some cases, staff would simply discover a box of unwanted or expired supplies and send it to the Supply Chain department where items were disposed of as waste, White recalled. Though expiration checks were to be logged on paper, this log was kept on a clipboard at the supply location. Expiration checks were performed on no particular schedule, and there was no way to monitor which locations had been checked other than physically going to the location and checking the log. In addition, the log did not capture any item detail, only that the audit was completed. These numerous inefficiencies led to inconsistencies in the audit process, she added.
Today, Supply Chain captures all of the necessary data electronically and has incorporated this technology into its multi-faceted automated processes. The results: As of the close of fiscal year 2018, more than 50 percent (based on item count) and almost 65 percent (based on dollar value) of PAR supplies underwent systematic, quarterly expiration audits. In addition, Supply Chain has identified products nearing their expiration dates that amounted to more than $50,000 in cost avoidance, according to Paolini.
CapTrack
Supply Chain re-engineered the manual capital program by custom developing an automated process from the ground up that promoted real-time, enterprise-wide transparency into all aspects of capital – from decision-making to expenditures.
“Our goal was to develop a comprehensive system that met all capital business needs across Tower Health verticals,” White said. “CapTrack involves the creative use of our intranet, automated workflows, coding languages, and Microsoft Office products.”
CapTrack uses complex automated workflows in conjunction with a single, electronic, “smart” intake form to determine the strategic direction and progression of the request, according to White. Information is collected through designated tabs on the form that align to the phase of the process, with automated notifications alerting appropriate parties when action is needed on their behalf. From request to payment and audit, CapTrack analyzes factors unique to the request, determines the appropriate automated pathway, and transitions the request through each phase of the process, all while providing comprehensive, real-time insight into every capital request through interactive reporting dashboards.
CapTrack monitors projects and individual requests through the entire capital lifecycle, from budget to acquisition, receipt, invoicing and payment. CapTrack also generates real-time, flexible reports on demand that include such details as status, department, facility, priority, fiscal year and dollar-level, among others. CapTrack also integrates with the ERP to report transactional dollars expended for invoicing and payment, as well as for accounting and budgeting, according to White.
CapTrack also provides each CFO with the ability to conduct “what if” scenario analyses for multi-year strategic planning and horizon scanning by modifying request parameters, such as anticipated purchase timeframe, priority-level, fiscal year, etc.
Robert Ehinger, Senior Vice President, Finance, appreciates the access, convenience and immediacy.
“By utilizing the system-wide real-time transparency provided by CapTrack, Finance has been able to determine and monitor the allocated, committed, and spent dollars throughout all the phases of capital,” Ehinger noted.” As soon as a payment is made by AP in the ERP system, it is immediately reflected in CapTrack.”
Mark McNash, Senior Vice President, Support Services, heaps high praise on CapTrack, too.
“CapTrack allows us to overlay our budget against acquisitions to provide an immediate view of our financial performance, both for individual initiatives and complex projects,” he said.
White, who applied her engineering expertise and mindset to CapTrack’s development appreciates how the tool is used and reflected on Supply Chain’s service-oriented reputation.
“CapTrack is focused more on gathering and reporting information, streamlining processes and providing the ability to track capital progression than on direct savings,” she told HPN. “All of the savings achieved through negotiations are reflected in CapTrack, but are not considered CapTrack savings. It is invaluable to an organization to know their financial position from a single portal across the health system in real-time.”
CSR: Contracting support requests
supply Chain also used automation to bring transparency and accountability to non-capital contract requests using its CSR: Contracting Support Requests tool to manage productivity and tasks required to “work” a contract, according to White.
Just like CapTrack, CSR operates through automated workflows, a “smart” intake form, and real-time dashboards, providing stakeholders with the tools they need to monitor the progression of contracts instantaneously throughout the process until the completion of the agreement.
A real-time productivity dashboard displays Supply Chain reporting for both tools, providing interdepartmental and third-party accountability for contract stage progression.
Per White, CSR:
- Assigns the task of working the contract to the appropriate Supply Chain team member, which is automatically based on the indicator in the ERP system
- Provides leadership with the ability to see that the contracts are moving along according to systematized, established expectations
- Provides reports to track the number of days the team member takes to work each stage of the process and how many contracts a team member is working on at once
- Evaluates and monitors productivity, ensuring workload is evenly distributed and processes are not becoming “bottlenecked”
- Enforces consistent contract processes across Supply Chain, requiring key information be entered before progressing to the next stage
iSCOPE
The Integrated Supply Chain Operations and Purchasing Exceptions (iSCOPE) board represents Supply Chain’s command center for performing online real-time inventory and distribution checks and visibility into all Tower Health facilities.
What’s noteworthy is that iSCOPE doesn’t supplant Tower Health’s Infor ERP, according to White.
“iSCOPE is a powerful tool that provides real-time transparency into Supply Chain operations,” she said. “iSCOPE doesn’t replace the ERP system; rather, it ‘picks up’ where the ERP system leaves off, enhancing the system, leveraging all of the data to support operations, and holding the staff accountable for performance in real-time.”
White quickly emphasizes that iSCOPE does not mean Supply Chain’s ERP module somehow falls short of expectations, dismissing a “lemons to lemonade” analogy. “We have developed enhancements that were thought to be impossible,” she noted. “Tower Health Supply Chain takes the statement ‘it can’t be done’ as a challenge to show not only how it can be done, but how it can be done using the tools already available to us – as in not spending any unnecessary money.”
iSCOPE is intended to provide complete transparency into and accountability for all Supply Chain functions, according to White. iSCOPE is an exceptions reporting system and has been established in Inventory and Sourcing to act as an alert manager for critical, key indicators for events that could potentially impact patient care and operations. Those indicators include urgent product requests, system downtime, PAR backorders, stockouts, unprocessed PAR orders, expiration checks, storeroom picks and overstocks, she added.
PAR-from-PAR replenishment
Because Tower Health’s ERP system did not support a PAR-from-PAR replenishment option, the Supply Chain team had to determine a way to use the current software without customizing Infor code, according to White. So they developed an ERP enhancement to avoid creating another perpetual inventory operation, which was complicated by three factors:
- The number of staff that would be required to maintain an accurate inventory due to the number of excessive ins and outs characteristic of an operating room environment.
- The non-secure location required for the clinical teams to pull cases without adequate ability to track and monitor the supplies as they were pulled.
- The half-mile distance from the general warehouse to the operating room locations.
“Creating a PAR that was able to replenish other PARs enables the Supply Chain team to reduce inventory and purchase items in bulk that would otherwise require [low-unit-of-measure] fees, thus saving $1.8 million for the health system,” Paolini noted.
Supply Chain’s efforts and accomplishments earned the Tower Health team the 2017 Infor Progress Makers Operational Excellence Award.
Epilogue: Infor has road-mapped Tower Health Supply Chain’s PAR-from-PAR replenishment solution with the potential to be incorporated into a future release, according to Paolini.
Pinpoint
Tower Health’s Supply Chain team proves that architects and engineers aren’t the only groups to use AutoCAD software to construct detailed and precise illustrations of equipment, floorplans and footprints.
In fact, White’s group used AutoCAD, Mixed Integer Linear Programming, ERP data, coding languages, and advanced analytics into a centrally controlled smart tool that functions much like a GPS for product locations. They call it Pinpoint for obvious reasons.
Pinpoint effectively enables clinical staff to locate the nearest PAR location that contains any identified product in the item master, even after standard business hours, according to White. A staff member can enter the ERP ID number or the manufacturer number – both readily available on the product identification label at its place on the PAR – and their current location, and Pinpoint will indicate the amount of product on the shelf at each identified location.
“Pinpoint identifies the PAR with the product needed that is closest to the identified location,” White explained. “Clinicians enter their current location into Pinpoint, which determines the closest PAR location with the identified item along with its PAR level.”
QuickTrack
Seeing how patients are “quick-tracked” in the emergency room, Supply Chain decided to apply that philosophy to evaluating process initiatives with a complexity rating of low to moderate and product initiatives with a rating of commodity and high-risk commodity, according to White. QuickTrack, which is part of iVAT, tends not to be used for physician preference items, she added.
The QuickTrack process allows an initiative to be vetted by all key stakeholders as it presents all pertinent information in a report similar to an Executive Summary, called the Prospectus (see the reference in the main story), and routing for approval via an eSignature solution, White explained. If all the stakeholders approve of the initiative through this process, the Supply Chain team begins the implementation process with no further evaluation needed at the monthly iVAT meeting. If even one key stakeholder does not approve the initiative through this process, the initiative becomes an agenda item on the next iVAT’s monthly meeting to further discuss. This empowers stakeholders to make fully informed decisions while ensuring standardization and cost-saving initiatives are processed quickly and efficiently without unnecessary use of team members’ valuable time, White added.
Tower Health Supply Chain leader shares team mindset, milestones for success
Reading, PA-based Tower Health’s Rita White, Vice President, Supply Chain, shared with Healthcare Purchasing News Senior Editor Rick Dana Barlow her team’s attitudes and motivations behind what, how and why they do what they do with valuable insights on what helps them succeed.
HPN: What’s the secret formula that makes a leader in supply chain management? How does your department implement that secret formula?
WHITE: Effective leaders are able to act as a two-way conduit between the strategic goals and needs of the organization and the skills of their team. Successfully achieving this two-way street involves continuous analysis of your team, their combined strengths, areas of opportunity and individual focus areas. Envision your ideal Supply Chain team and compare it against your current one. What skill sets are currently represented on your team? What is still required? What skill sets are being underutilized? By answering these questions on a regular basis, leaders are able to develop a roadmap to build a fluid, adaptable force capable of rapidly adjusting to meet the needs of an ever-changing environment. This mentality is especially applicable when there are FTE openings — a true leader does not simply hire a replacement. Rather, they hire people capable of propelling their department forward.
The next big trend in healthcare supply chain management will be...[fill in the blank]. Why?
Supply Chain was recognized for this award in part because of our development of iSCOPE to provide insight and accountability into our inventory functions. It is our belief that tools like iSCOPE will be “the next big thing” in Supply Chain, taking clinician and patient support to unprecedented heights. We intend to take iSCOPE to the next level of virtual management, designing it to provide real-time insight into every aspect of Supply Chain throughout the enterprise.
Some in the “C-suite” have criticized supply chain managers for being too technical and not strategic enough to “join their club.” Do you agree? Why?
The culture at Tower encourages collaboration at all levels of the organization, so this has never been an issue for us. Effective Supply Chain support of health systems requires that leaders are strong strategists with technical skill sets and tactical visions for the department and organization.
How can consulting firms, distributors and GPOs contribute to the performance of your internal supply chain management expertise without overshadowing the department or usurping control?
We have not experienced this difficulty at Tower Health. Our distributors are part of the team — they know what is expected of them and are involved in the “hands-on,” daily activity of the department. Our GPOs supply us with spend data and assist with contract discrepancies; it is the responsibility of the Supply Chain team to apply the data according to our needs. Tower Health partners with AllSpire and its member hospitals to go beyond the traditional GPO and achieve improvements for all members as a whole.
What specific project did your department complete where you felt they didn’t live up to your expectations and one where you felt they exceeded your expectations?
As a leader, I have very high expectations of myself and hold the Tower Health Supply Chain team to the same level of expectations. Even so, I am impressed every day by the creative solutions we devise to the most complicated challenges facing the industry. No matter the challenge, our team finds a way to develop a solution — if we can’t go left, we go right. The team will exhaust every avenue to achieve our goals, challenging perceived limitations and applying outside-the-box thinking to implement the best solution.
In your opinion, what is your department’s toughest administrative challenge? How might you solve it?
The required process surrounding all types of contracts — supplies, capital, purchased services, etc. — is time-consuming, owing to the challenge in standardizing and managing contracts across the enterprise, the redlining of terms and conditions and strategic management of contracts across the enterprise. Vendors have brought a new layer of complexity to the contracts by requiring compliance across contract categorization, thus creating a “domino effect” for contracting decisions.
What is your department’s toughest operational challenge? How might you solve it?
Clean, comprehensive data is the cornerstone of effective decision-making, but pertinent data does not live in a vacuum. Being able to obtain, cleanse, and effectively merge data from multiple sources presents a significant challenge to all Supply Chain departments. Available data is often self-contradictory, incomplete, or blatantly inaccurate, leading to potentially misguided business decisions. Tower Health Supply Chain confronts this challenge by maintaining the highest standards for internal data, such as ERP data, and enforcing rigorous analysis of data gathered externally. It is essential for our team to ensure incoming data sources have been thoroughly evaluated in adherence to our standards.
Another operational challenge was presented when Tower Health opened a new surgical tower at Reading Hospital in 2017. There was a significant distance between the surgical tower on one side of the hospital campus and the inventory storeroom on the other side. Effectively supporting the OR would be nearly impossible with the amount of distance between the two locations. The most practical solution would be to create a second location to house supplies nearer the operating room, which would allow Supply Chain team members to replenish the OR PARs from the second location. However, the challenges of setting up and maintaining a second Perpetual Inventory far outweighed the benefits, and our ERP system did not support replenishing a PAR location from another PAR location. To address this challenge, Supply Chain developed a PAR-from-PAR replenishment solution, effectively leveraging our ERP system to implement a solution that was previously considered impossible.
What are your top three priorities for the remainder of 2019 and for 2020?
As always, Supply Chain’s top priority is to support the strategic goal of financial discipline across the six Tower verticals in support of cost-effective, high-quality healthcare.
Tower Health has recently integrated all member hospitals into a single ERP system and is now focusing on the integration of EPIC. Supporting this integration will be a top priority for Supply Chain until 2020.
Additionally, with the integration of the ERP system came the merging of copious amounts of data, much of which is incomplete or inaccurate. Supply Chain prides itself on maintaining pristine data to support conscientious decision-making. Consequently, significant effort will be expended over the upcoming months to bring integrated data to the same level of accuracy.
How does the CEO view your department? Does he or she see it as a strategic function or a support service? What resources can the department count on and will they come every year — and not just in response to clinician complaints?
Tower Health leadership has been exceptionally supportive of the Supply Chain department, demonstrating the confidence in the department that allowed us to build the team required to provide the innovative solutions to support Tower Health.
What are some practical, common sense ways that supply chain managers can keep patient satisfaction in mind as they’re performing their duties?
All health system employees are here for our patients, whether or not we have direct contact with them on a daily basis. They are our primary focus and we are called every day to demonstrate our commitment to their wellbeing and care.
If you could change one C-suite and clinical (physician/nursing) perception of your department, what would it be and why?
Tower Health C-Suite has demonstrated a recognition of the value that Supply Chain brings to the enterprise and embraced the evolution of the team.
How can supply chain managers collaborate with other departments and professionals and convince them that their decisions are based on the financial health of the organization and not in denying them quality products or dictating patient care as the clinicians might tell the CEOs?
Decisions regarding products used within Tower Health are made collaboratively through iVAT, which are co-chaired with physicians and departmental directors. Throughout this process, clinicians often want to know how the health system will be impacted financially by an initiative, so they can make conscientious decisions about what is best for both the patient and the health system. Supply Chain is considered a “non-voting” member of iVAT — rather than “tell” clinicians what products to use, Supply Chain presents all of the vital information and projects cost impact regarding initiatives in a consistent, sophisticated layout through the Prospectus. The Prospectus outlines the potential financial impact to the health system, as well as all other clinical and nonclinical information pertinent to the initiative, in a meticulous, consistent format, setting the environment for solid, informed decisions from all perspectives.
What advice do you have for professionals outside of healthcare wanting to enter into the field of healthcare supply chain management (whether college students or from other industries)?
Healthcare is unlike any other industry. Although many Supply Chain team members do not interact with patients on a daily basis, lives literally depend on us performing our role. We do not simply leave our jobs at the end of the workday — we are here for our clinicians and patients 24/7. To succeed in the healthcare industry, one must have an unwavering commitment to helping others and a willingness to do what is necessary to provide unceasing support to our patients and clinicians while being financially accountable.
In a previous life (1999-2003) you took a detour from healthcare supply chain management to run your own company as President of Linko Engineering Inc., South Bend, IN. What useful and valuable lessons and skills did you learn in that position that you were able to bring to the healthcare supply chain once you returned?
I grew up in an environment where I learned how to read blueprints and develop process improvements as part of my everyday life through my family’s business. Today, I still consider myself in an engineering environment, as we apply a continuous-improvement mentality within Supply Chain. We employ logical, outside-the-box thinking to develop creative, innovative solutions to the challenges faced by health systems. We continuously question assumed limitations, breaking the mold by challenging our own perceptions and developing solutions that would be often be considered impossible.
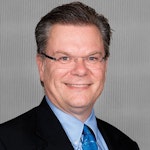
Rick Dana Barlow | Senior Editor
Rick Dana Barlow is Senior Editor for Healthcare Purchasing News, an Endeavor Business Media publication. He can be reached at [email protected].