The core Laboratory at many hospitals around the nation may not enjoy Supply Chain’s expertise in helping to control expenses as much as Surgical Services, for example, but that doesn’t faze Supply Chain executives at two healthcare organizations on either coast.
They’re already involved and have been partnering with the Lab for several years.
In fact, for David Boyce, CMRP, Vice President, Materials Resource Management, Carolinas HealthCare System, Charlotte, NC, quipped that their efforts twisted the typical.
“Frankly, for our system, our success in the Lab has allowed us to be invited into the Operating Room,” he chimed. “Success breeds success and allowed us to overcome historical bias. As a rule, every item — whether it be in the OR or the Lab — has a story, some more complex than others. Once the story is understood, supply chain tactics can be applied. These tactics are where Supply Chain shines and provides value to the OR or Lab in increased performance, while returning clinical staff to the top of their license.”
During an educational session at the annual AHRMM conference in 2014, Boyce recounted how his team was invited to manage the supply chain for Carolinas’ new clinical reference or core lab.
“Our team controls the entire supply chain through a two bin Kanban signaling system,” Boyce said. “Before we stood the system up, we had solved the issues with refrigeration and lot control and have built standard work processes around these unique items. Supply chain management of all products used to produce patient lab results has increased fill rates, reduced held inventories and increased job satisfaction for lab teammates. As the result of this success at our central reference lab, we have expanded the model to our facility labs using lessons learned for the unique lab items.”
Based on that success, Materials Resource Management expanded its influence into the OR, Catheterization Labs and Neonatal Nurseries, according to Boyce. “Our motto that drives our team is, ‘When you reach for it, it will be there,’” he added.
Across the country on the West Coast, the Supply Chain and Laboratory teams at Seattle-based Virginia Mason Medical Center fostered their partnership in a different way.
Around the turn of the millennium, Virginia Mason embarked on a facility-wide “world class” performance improvement initiative based on the principles of the Toyota Production System, which includes just-in-time distribution. Supply Chain and the Lab signed on as early and independent adopters to what the organization called the “Virginia Mason Production System.” (Editor’s Note: Virginia Mason earned Healthcare Purchasing News’ 2004 SPD Department of the Year award, partly stemming from its implementation of the VMPS.)
Virginia Mason’s “World Class Management” initiative involves three components, according to Linda Hebish, Administrative Director, Supply Chain: Management by policy, daily management and cross-functional management.
“Wherever or whenever Supply Chain works to improve supply operations processes, we engage in cross-functional management,” Hebish told HPN. “As VMPS leaders, both the Lab and Supply Chain work hard to promote the cross-functional management component.
“Collaboration, respect for people, reducing the burden of work of staff and continuous improvement are just a few of the tenets of VMPS embraced by these two departments,” Hebish continued. “Executive and senior leaders within the Lab and Supply Chain have attained the highest levels of VMPS competency. All supervisors, managers and directors, plus several frontline team members, excel in the basics of VMPS. This is evidenced by their departmental commitments to daily kaizen — see the problem, capture the problem, work together on ideas to resolve, test, implement, and monitor for success.”
Ensuring staff and patient satisfaction drive ongoing VMPS efforts.
“One motivation is to eliminate unnecessary processes thereby removing the burden of work from the worker,” Hebish said. “Leaders work with the frontline to help them see the non-value-adding processes, together they design better processes and increase employee satisfaction in the process when leaders follow our respect for people behaviors. At Virginia Mason, the patient is the focus of our strategic plan. We improve our processes to improve our patient experience. If the change in process is linked to improving patient safety, quality, or experience, team member motivation follows. VMPS is a cultural transition requiring immense leadership, persistence and perseverance.”
In 2013, Supply Chain launched a comprehensive approach to value analysis, creating six Value Analysis Teams, of which the Lab was one, according to Hebish. The initial focus was pricing collaboration.
“Over the course of the next few years, the teams reported success with product conversions and distributor conversion, and reduced pricing on five reagent agreements,” she recalled. “However, they continued to see their medical supply expense increase as measured against gross revenue, by a staggering 20 percent. Some of this is attributed to rate decreases but the cost of medical supplies, excluding blood products, continued to rise.”
Budget constraints motivated the Lab to commit to better manage their medical supply expenses, Hebish said. The relationship with Supply Chain only blossomed from there.
“Supply Chain has always been involved with the Lab at Virginia Mason — at first very minimally with a dedicated, centralized buyer for the Lab,” Hebish said. Then efforts expanded to include all product acquisitions.
During the latter part of 2016, the Lab leadership began digging deeply into their supply expense, Hebish noted. They set a goal for 2017 to improve supply chain management and reduce inventory. Consequently, Supply Chain is providing tools, guiding principles, education and ongoing support as the Lab moves closer to a just-in-time supply delivery system, according to Hebish.
“Over the past 26 months, Supply Chain has developed organizational standards, guiding principles and tools to create an environment where we can deploy operators to any area and continue to be successful because we have supply management standards,” Hebish said. “The Lab understands the importance of utilizing standards to create teams of multi-skilled operators and naturally engaged with Supply Chain for assistance with their supply initiative.”
Even if both departments didn’t embrace and implement the VMPS, any collaboration would have to be based on and rooted in trust, Hebish insisted.
“The key is proving that Supply Chain is a reliable, trust-worthy partner,” she said. “If this can be done with a product conversion or a pricing negotiation in collaboration with Lab counterparts, the foundation for the relationship is set.”
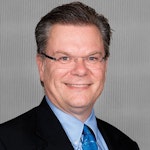
Rick Dana Barlow | Senior Editor
Rick Dana Barlow is Senior Editor for Healthcare Purchasing News, an Endeavor Business Media publication. He can be reached at [email protected].