Manufacturers, distributors and retailers that view products as assets that generate revenue have mastered how to maximize their return on investment.
This tends to involve incorporating some of the latest and newest logistics and material handling technology or implementing effective techniques that rely on existing technology to move product through their supply chains. Examples include, but are not limited to, the following: automated/vision-guided vehicles, automated storage and retrieval systems, conveyor systems, drones, hand-held/wrist scanners, horizontal carousels, pallet rack systems, real-time location systems, robotic arms for “cobotic” picking, vertical carousels and vertical lift modules, pick-to-order fulfillment solutions, virtual reality or augmented reality headsets and voice-directed picking systems, among others.
Some, but not all, may be adapted to and geared toward healthcare provider organization warehouses and storerooms. So what might hospitals and other healthcare facilities that may be part of integrated delivery networks (IDNs) and rely on centralized distribution or consolidated service centers learn from those in manufacturing, distribution and retail corporations — both inside and outside of healthcare?
Healthcare Purchasing News reached out to a host of provider and supplier supply chain executives about the innovative products and technologies used for material handling in other industries that would be useful in hospital or IDN storerooms and warehouses and why.
After two years in development Indiana University Health recently opened an off-site centralized distribution center to service its 18 hospitals and hundreds of clinics, according to IU Health. The “Integrated Service Center” sports many of the trappings of a large-scale distribution warehouse, including an electronic, software-directed robotic picking system that Dennis Mullins, Senior Vice President of Supply Chain Operations, hails as innovative for his organization and the industry.
Robotic picking systems that automate and speed up the process of selecting inventory for delivery, represent a “significant innovation,” Mullins told HPN. “The systems are computerized and include software that can be customized to a user’s specific needs.
“Robotic pickers have the ability to move more product through the picking process than by humans alone, with higher reliability and accuracy than doing it the traditional way using people and forklifts,” Mullins continued. “The robotic technology works at double or triple the rate of a human walking the shelves or driving a forklift to bin locations. Supplies represent 25 to 30 percent of a hospital system’s operating expenses, so creating savings in the supply chain can be significant to the organization.”
Mark Wheeler, Director, Supply Chain Solutions, Zebra Technologies, urges Supply Chain professionals to do their homework before investing in higher-tech options for their storerooms and warehouses, focusing on tradeoffs based on operational characteristics.
“They should start by defining their operational requirements as realistically as possible and then project those requirements over the design life of the facility,” Wheeler noted. “The typical time frame for this is three to five years and the requirements take business metrics and help translate them into logistics metrics. They should also consider how many orders per day, what the average and peak number of orders would be, what products need storing, stock-keeping unit (SKU) and all their physical characteristics, packaging variants, volumes, temperature zones and regulatory restrictions (such as Class II Pharmaceuticals).
“Another question of importance is what is the level of certainty in these numbers?,” Wheeler continued. “High degrees of certainty allow the designer to consider less flexible but potentially more optimized material handling solutions. Calculating these metrics will be fundamental to driving the design decisions around material handling technology and techniques. Skipping this step or minimizing the effort leaves subsequent design decisions ungrounded in the realities of the business. The size and complexity of the operation will typically dictate both the rigor of the data analysis and the level of technology that’s appropriate for the operation.
Wheeler listed and outlined some of the design trade-offs as including:
- Capital versus Operational Expense: Capital-intensive solutions, such as automatic storage and retrieval systems can reduce labor costs on an ongoing basis.
- Operational Flexibility: This is one criterion where recent innovations in mechanization outshine their older counterparts. New automated storage and retrieval system (AR/RS) solutions and “cobots” are flexible enough where investing in them is less likely to hamstring operations should the volume or materials change in unforeseen ways.
- o In terms of what can be easily stored (size, shape, temperature zone)
- o In terms of scalability and throughput (orders, full vs broken case, order turnaround time, peak volumes)
- Space Utilization: Healthcare storage must be secure and environmentally controlled and this typically requires expensive space. Choosing solutions that will utilize the space effectively while allowing for efficient access for ins-and-outs is key. Carousels and vertical carousels can store products efficiently and securely while utilizing the vertical cube.
- Wearables: Human-oriented solutions, such as wrist-worn mobile devices coupled with a wearable scanner, are not only cost-effective but can also achieve near 100 percent accuracy. The traceability of lab specimens, lab equipment and other clinical assets is a growing requirement and wearable scanning is critical to verifying accuracy. Nowadays, product is not only lot-controlled but also serialized so tracking the movement of materials to the point of use is needed and wearable scanning is the only way feasible way to do this for each order line. Voice-directed modes for data presentation and capture also can be added to these solutions making them easier for clinicians to learn and use. Heads-up display solutions are relatively new to logistics but have also been shown to have operational value and could be translated into the healthcare environment.
Ultimately, it’s the details of the workflow that will drive these solution design decisions. The goal is to make the technology work within the physical workflow as seamlessly as possible. Getting this right will provide the best results both in productivity and in accuracy.
- Drones: Drones have been shown to be a viable way to verify inventory in bulk-storage environments or in rack storage where the materials are clearly barcoded or RFID-tagged. While healthcare distribution facilities may have some bulk storage, most of the complexity and cost in the operation is because of broken case or piece handling.
- Automated Guided Vehicles (AGV): There are a growing number of AGVs in all shapes and sizes that can transport projects throughout the warehouse. From pallet-level down to individual pieces, there is an AGV for every job. Lithium-ion batteries have helped make these new AGV’s smaller, lighter and safer than their predecessors. They are essentially replacing other forms of transportation such as conveyors, carts or lift trucks in the operation.
Implementing material handling technology within end-to-end supply chain logistics will enable healthcare professionals to spend more time with patients and provide better care for better outcomes, according to Norman Brouillette, Vice President and General Manager of Technology and Healthcare, Ryder System Inc.
Brouillette cited several innovations that can be useful to hospitals and IDNs, including:
- Autonomous material handling equipment: This equipment can self-navigate within a warehouse after a one-time mapping exercise of the facility. This autonomous capability can be applied to various types of equipment, including mobile robots that can move a case and forklifts that can move pallets.
- Industrial robotics: These robots utilize different attachments to perform tasks utilized for receiving and or shipping activities.
- Sensors: Sensors monitor the activity, condition and events in the use of material handling equipment, human resources and the facility. These sensors can be active RFID, Bluetooth (BLE), LORA or other types of radio signals.
Third-party logistics companies can help hospitals create a more efficient end-to-end supply chain over the long-term, Brouillette insisted.
“Today, health care professionals and caregivers double order stock because of uncertainty under an outdated system,” he said. “Third-party logistics [companies] can provide the infrastructure hospitals need for reliable assurance from best-in-class warehouse management and inventory systems.
“These management systems can be integrated just as it’s done in retailing, automotive and consumer packaged goods,” Brouillette continued. “From an end-to-end logistics standpoint, the capabilities we previously mentioned can bring products at the point of delivery all the way through to the operating room of a hospital. This increases the quality of support among hospital staff to better equip them with the tools needed for the patients under their care.”
Brouillette promoted how various material handling innovations can help healthcare organizations improve supply chain operations.
- Autonomous material handling equipment: In the past, delivery systems were dependent on manual tasks. Now, automated guided vehicles can be programed to run independently in off-shift hours and can be used to replenish storerooms within the hospital or delivered from the storeroom to other defined areas.
- Industrial robotics: Industrial robots can perform the storage, deliveries, and stocking of supplies and materials. Also, robotics can be used to prepare the operational and therapeutic kits required for medical examinations and surgeries.
- Sensors: Sensors provide the visibility caregivers and purchasing personnel need to account for the level of their inventory. Also, sensory technology would give hospitals and IDNs the capabilities to monitor the environmental conditions of the storerooms, provide security functions, and track the location of supply chain resources and equipment.
“Through a proper supply chain logistics system with scanning proficiencies, hospitals and IDNs can account for re-orders, expiration dates, FIFO and FEFO in a coordinated, real-time operation,” he added.
Jeff Christensen, Vice President of Product, Seegrid, promoted the use of third-party expertise, including “application engineers, customer success consultants, deployment specialists and service and support representatives…from initial application development to regular monitoring and analysis of operations.”
Christensen also advocated for self-driving vision-guided vehicles (VGVs) and fleet management software to link all of the moving parts in the chain.
“Any company moving heavy loads around their facility that values throughput productivity, employee safety and labor cost will benefit from vision guided vehicles — including healthcare providers,” Christensen said. “Unlike old AGV technology, the Seegrid VGVs are built for flexibility, enabling companies to retain routes in-house and deploy the vehicles in minutes. These self-driving vehicles work tirelessly alongside humans to greatly improve the operational efficiency of any large warehouse or distribution center. Our self-driving tow tractor and pallet jack use cameras to navigate autonomously.”
Fleet management systems like Seegrid Supervisor provide real-time status updates and performance metrics to help supply chain managers optimize their VGV fleet and connect their smart factories, according to Christensen. “They also enable users to dynamically re-route VGVs with remote calling to any location and to dispatch VGVs to a different area to support changing warehouse demand,” he continued. “Any healthcare organization that relies on a supply chain to move materials will benefit from the data-driven decisions that become possible with a fleet management system.
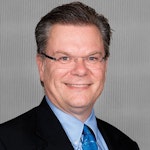
Rick Dana Barlow | Senior Editor
Rick Dana Barlow is Senior Editor for Healthcare Purchasing News, an Endeavor Business Media publication. He can be reached at [email protected].