When a disaster strikes is not the time to start thinking about planning your supply chain strategy to weather disasters.
Historically, some facilities learned the hard way about being unprepared as hurricanes, tornadoes, superstorms, wildfires, infectious outbreaks and terrorist attacks, among other maladies, disrupted their supply chains by cutting off or destroying available transportation routes to move products and equipment and provide necessary services to their facilities.
Disasters don’t just cripple supply chains, however; they also clog clinical care access in the emergency and operating rooms and clot sterile processing’s efforts to provide the clinical areas with safe and ready-to-use devices, instruments and equipment.
Yet as operations seemingly spiral out of control, fraying nerves and reason beset by panic and despair, Supply Chain — almost like the U.S. Postal Service — is expected to deliver. And Supply Chain can’t do that without suppliers on the other side of the “chain” wrestling with their own issues to produce and move products.
Of course, many will acknowledge — somewhat logically — that a provider or supplier cannot be fully prepared for any and every problem that may arise. But, by and large, providers and suppliers have learned enough about disaster historicity to approach seasonal and even unexpected crises like an annual flu shot.
Ready or not, we are
Disaster-readiness generally translates into a tested and working emergency response plan, regardless of supplier or provider.
For example, on the supplier side Cardinal Health roots a core philosophy to its emergency response, according to Sean Halligan, Senior Vice President, Supply Chain Operations.
“We have a very strong ‘do the right thing’ value in our organization that tells us to put medicines and supplies in the spots where they are needed most,” Halligan said. “In the spirit of our team’s work, and the knowledge of our importance to healthcare, we do whatever it takes — especially in a disaster situation — to navigate and help customers.
“It doesn’t matter if we’re responding to a 500-bed hospital, a 50-bed clinic, an independent pharmacy or a retail chain, Cardinal Health prepares in the same way to address an impacted disaster area,” Halligan continued.
Just as airline flight attendants instruct passengers to don their own oxygen masks before helping others, Cardinal Health works to ensure its own teams are safe and secure first as they will be the company’s front line to customer clinicians, administrators and communities, according to Halligan. “They ultimately keep our supply chain intact,” he added.
The company maintains 21 forward distribution centers strategically placed around the country that deliver fulfillment capabilities for more than 40,000 items, including medications, over-the-counter products and critical supplies such as injectables, Halligan explained.
“All distribution centers have 100 percent redundancy, backed up with on-site generators in the event of power loss. In addition, we have contracts with key providers in each area to ensure generators can be re-fueled if they are needed and our facilities can be quickly repaired if damaged.”
Cardinal Health demonstrates supplier flexibility by also operating a fleet of “temperature-controlled trailers that can act as mobile distribution centers to store temperature-sensitive products,” he said. “For example, if a building was damaged, we could quickly recover cold-chain products and put them into storage trailers — ensuring we still have supply in the region where it is needed.”
Meanwhile, on the provider side, the two-hospital, Savannah, GA-based St. Joseph’s/Candler Health System remains battle-ready to handle crises, which in the southeast tends to involve hurricanes, according to Joe Loya, Director, Purchasing & Distribution.
“At my facility we have a Supply Chain Disaster Plan that initiates three-to-four days prior to the hurricane threat,” Loya told Healthcare Purchasing News. “At that point we order an additional week of supplies for all areas. Any needs beyond that would be harvested from ‘procedural’ departments, such as OR, Cath/EP Lab and Imaging.”
St. Joseph’s/Candler operates under a low-unit-of-measure/just-in-time model with pre-assigned “A” team members and “B” team members with lists updated prior to hurricane season, Loya indicated. “The goal of the organization is to evacuate as many employees and patients as possible. Therefore, Supply Chain only staffs a group of four-to-five employees that will be supported by B-team members once access to the city has been relieved. Working closely with CEMA [Chatham (County) Emergency Management Agency], our organization will determine whether we need to discharge patients, close a hospital and consolidate to one hospital. The hospital that we consolidate to has the latest construction-related attributes that can withstand hurricane-force winds.”
During hurricanes Matthew and Irma, St. Joseph’s/Candler Health consolidated hospitals twice, according to Loya. Because the hospital in which the organization consolidated services does not normally manage Women’s Services, they had to equip the facility with Labor & Delivery-related supplies. “We had multiple deliveries and not a hitch,” he said. “General patient care supply support also had no interruptions.”
Loya emphasizes that “this plan has been tested and works.” But they also maintain a secondary disaster preparedness plan with its distributor Owens & Minor to air lift supplies to the facility post-disaster, and they have an agreement with the Hunter Army Airfield military base for support as needed, he added.
Such extensive readiness is necessary if St. Joseph’s/Candler wants to fulfill its goal to “open dire services to the community related to dialysis, ED, ICU and imaging” to care for patients and meet their healthcare needs, according to Loya.
If the crisis is pandemic-related versus weather-related, the organization carries specific inventories related to that pandemic issue, including Ebola, Loya noted. “We physically inventory those items and cycle them so that there are no expirations,” he said. “Fortunately, we have practiced pandemic/Ebola response, but have not actually been tested.”
On the pulse
Just as it advises its customers, Cardinal Health develops and operates a “Business Resiliency Plan,” according to Halligan, steeped in best practices to make sure those in need get critical medications and supplies during emergencies.
“To ensure we are prepared, every location and team must have a plan entered into our data repository,” he said. “This plan includes elements from teams across the enterprise, including EHS [Environmental Health & Safety], Global Security, Business Continuity and IT.” (See sidebar for Cardinal Health’s business resiliency plan best practices.)
Timing is critical, Loya emphasizes, particularly before an anticipated crisis emerges.
“Our response during hurricanes is early enough that our distributor, which is two hours away, can respond in time,” he said. “Orders are placed the morning of and shipped that night. Due to the inability of the distributors to drive during high winds — 30 miles an hour or more — we enact our procedure early and stage supplies.” (Editor’s Note: The Saffir-Simpson Hurricane Wind Scale classifies a Category 1 storm as having a minimum 74-mile-per-hour wind speed.)
Even then, St. Joseph’s/Candler has a secondary contingency and a tertiary contingency, too. For example, if the distributor is unable to deliver from its primary warehouse due to damaged facilities or available transportation routes it will deliver products from a back-up location four hours away, Loya indicated. If even that became an issue, Loya’s organization would work with its local military services branch to support the facilities with needed supplies via its military base.
Loya admits that having access to a military base and personnel assets is a boon for St. Joseph’s/Candler Health and its patient community. The provider’s Safety Officer serves as the liaison with local military representatives as part of CEMA and works to arrange the base’s support when needed, he said. But this covers necessary supplies.
“As for non-stock or special order items, the OR staff … along with our departmental buyers will work with ancillary departments to ensure that any special order items are requested and shipped,” Loya continued. “During a hurricane, the hospital will cancel all elective cases and close down to ride the storm out. For other disasters, such as the sugar refinery explosion in 2008, we report to the hospitals and find any spare equipment that may be needed for the ED. We also stay accessible for any supply needs and will use our back-up supply dispensing department, or [procure] from other departments if needed.”
Loya says that his organization, as well as suppliers and their third-party carriers, monitor wind speeds closely. In fact, “potential increases in wind may trigger initiating our disaster plan,” Loya admitted. “The last hurricane (Michael, October 2018) that we had threatening this area started with high winds. I activated the Supply Chain disaster plan well before the health system activated the organizational plan, due to wind speed. Ordering in supplies that can result in increased cost impacting monthly financials is better than not having supplies, so knowing that winds are a major factor, activating the disaster plan is very time-sensitive.”
Locked and loaded
Disaster-readiness represents serious business for both suppliers and providers.
“From wildfires and tornadoes in the United States to tsunamis and cyclones around the globe, Cardinal Health and its employees have sprung into action, time after time, to help those in urgent need,” Halligan said. “Since 2000, Cardinal Health has donated more than $155 million in medical and pharmaceutical products, which are often the most needed items in times of disaster.” The distributor partners with four organizations that have experience in getting medical supplies quickly to those in need: AmeriCares, World Vision, MAP International and Heart to Heart International. (Editor’s Note: For specific examples, visit https://www.cardinalhealth.com/en/about-us/corporate-citizenship/community-relations/employee-involvement/hurricane-relief-efforts.htmlinement/hurricane-relief-efforts.html)
St. Joseph’s/Candler Health’s distributor operates a local warehouse with the purpose of receiving, storing and distributing private-label supplies from cargo freight tankers. Savannah is located about 20 miles from the Atlantic coast.
“They use that warehouse as a hub, and then ship to the distribution centers,” Loya indicated. “Just prior to a hurricane, the distributor gave us access to that inventory, and we drove a truck to it and loaded up on general supplies, such as gloves, gowns, masks.” What’s also noteworthy is that the healthcare system’s distributor automatically sends St. Joseph’s/Candler Health pallets of water at the onset of hurricane season.
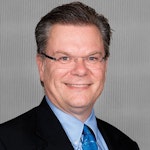
Rick Dana Barlow | Senior Editor
Rick Dana Barlow is Senior Editor for Healthcare Purchasing News, an Endeavor Business Media publication. He can be reached at [email protected].