Steering supplies on a steady track to needed destinations
Many hospitals and healthcare facilities have turned to new avenues of sourcing, storage and shipping of personal protective equipment (PPE), lab tests, medications, ventilators and other high-demand items needed to help protect healthcare workers and care for patients.
Jeff Schroeder, Director, Distribution Operations, LeeSar, expressed, “In 20-plus years of working in the medical supply distribution field, I’ve seen a number of crises come and go: swine flu, bird flu, Ebola and quite a few hurricanes. However, I’ve never seen anything as disruptive as COVID.”
Freight, shipping and logistic companies have shifted their operations to help enhance safety throughout their workforce and for customers, ensure on-time deliveries of vital medical supplies and equipment, as well as prepare for future catastrophic events.
Federal movement of product from overseas
The pandemic has caused significant challenges in manufacturing and shipping of critical supplies and equipment from China and other international areas. Production stalled, travel became restricted and shipping delayed. Federal agencies, such as the U.S. Food and Drug Administration (FDA) and the Federal Emergency Management Agency (FEMA), acted to expedite product movement to the U.S.
The FDA’s Office of Regulatory Affairs (ORA) focuses on safety and efficacy of product coming into entry.
“Many of the medical products our healthcare workers and hospitals need to battle COVID-19 come from overseas, which makes the FDA’s ORA work imperative to ensure products are moving as quickly as possible through the ports of entry,” the FDA stated. “ORA protects the supply chain in two equally critical ways: first, we help ensure safe products are coming in and second, that illegal, dangerous and fraudulent products do not get into the country. The FDA is using the risk-ranking technology tool PREDICT on commercial shipments, numbering in the thousands, to release packages with accurate documentation and shipping contents in minutes rather than days.”1
A national network and a FEMA taskforce concentrate on quick distribution of product to public and private sectors.
“To more effectively adjudicate resources throughout the nation and private industry, a National Resource Prioritization Cell was established to unify government and private industry prioritization recommendations which will inform federal, state and private sector operations,” FEMA reported. “The Supply Chain Task Force is working with the major commercial distributors to facilitate the rapid distribution of critical resources in short supply to locations where they are needed most. Working together, we are able to efficiently distribute these vital resources to hospitals, nursing homes, long-term care facilities, pre-hospital medical services, state and local governments, and other facilities critical to caring for the American people during this pandemic.”2
Product procurement leads to sourcing alternatives
Hospitals and facilities have found themselves racing to locate and bring in the products they desperately need to care for patients.
Steve W. Martin, Senior Vice President, Ryder Dedicated Transportation Solutions, points to helping customers manage the movement of high volumes of product.
“When the pandemic began to impact North America, we experienced an initial surge of volume with multiple healthcare customers, which was largely due to the uncertainty of what was to come,” Martin expressed. “There were concerns about inventory and with some states closing their borders to interstate travel. In one instance, we had a major healthcare distributor shift large quantities of medical beds, wheelchairs, and walkers downstream in their supply chain. This created an initial surge of volume in the short term but has leveled off over the last several weeks. We were able to work with that customer to provide incremental capacity to meet the demand.”
“Alternate sourcing strategies are now a real option for GPOs to consider,” Watson emphasized. “Extended arms of healthcare organizations, such as AHRMM, have stepped up to provide alternatives and vet suppliers as quickly as possible. The idea that a hospital can only source from one or two vendors is now a thing of the past.”
“We will need to help hospital procurement and supply chain teams at hospitals balance the benefit of single sourcing for savings versus using multiple sources to prevent from having all their eggs in one basket,” Romanelli stressed.
“Because of shortages in the domestic supply chain, many of our customers have been forced to source products directly from overseas manufacturers,” Carroll explained. “A significant issue with this approach is that buyers rarely have the logistics experience required to ensure the product is being delivered in a timely and cost-efficient manner. VPL has been working closely with these customers to arrange for international shipping, so they can stay focused on sourcing rather than logistics.”
Adjusting workspaces, hours and practices
Ryder’s Martin calls out several changes in their operations, including additional storage, hours, transportation and discounts.
“We have established pop-up warehousing to safely store essential supplies and have increased operating hours to handle the demand,” Martin stated. “We’ve re-deployed trucks and drivers from non-essential businesses experiencing significant reductions in volume and production shutdowns to essential businesses experiencing extreme surges in demand. We pulled together a pop-up fleet of 60 of our rental vehicles from 45 different Ryder facilities in just a few short hours to support a customer that urgently needed to distribute critical medical supplies, pharmaceuticals to doctors’ offices and pharmacies, assisted living facilities, and people’s homes. Additionally, we have tapped Ryder’s transportation management and freight brokerage divisions, where we leverage our buying power with thousands of reliable for-hire carriers on behalf of customers who are experiencing surges in volume and need the additional capacity.
“We’ve been working proactively with customers in retail pharmacy to shift their supply chain strategies and inventory placement to ensure they can make time-critical deliveries of medications and personal protective equipment. Ryder has also offered discounts on commercial rental rates to companies transporting medical supplies and other customers contributing to COVID-19 relief operations in the U.S. and Canada.”
“Several clients have secured incremental warehouse space, redefining the mission of existing space, leasing space, or working with the commercial community to secure space to stockpile pandemic supplies. We had several clients looking to mitigate over-burdened facilities with COVID-deceased bodies. Changes to process and refrigerated shipping containers provided some capacity relief,” Redding described.
Increased immediate shipping needs have resulted in increased hours for its staff, says, VPL’s Carroll.
“VPL is nimble enough to provide special services as needed by our customers,” Carroll addressed. “The only real difference now is the increased volume of requests. With so many of our customers currently working with reduced staff, they are naturally working longer hours. We have significantly increased our afterhours coverage to ensure we are always available to take care of any last-minute challenges they might be facing.”
LeeSar has enabled staff to assist each other and the business.
“Due to the pandemic, our fueling source has changed their hours of operation,” LeeSar’s Smith said. “Daytime drivers have been asked to ensure trucks have enough fuel for the evening and night shift drivers.”
Schroeder of LeeSar, added, “If one department is slow there may be a chance to cross-train and shift that labor where it can be better utilized.”
“OptiFreight Logistics has seen an increased need for same-day movement of items such as PPE and diagnostic samples, to urgently get these critical shipments to the right sites of care,” Laber shared. “Many providers have also launched same-day home delivery of home health supplies and medications, so that patients may avoid going out in public to pick up the items they need.
“Some of the ways we have been serving customers differently include:
- Bulk/large freight orders
- Domestic and international shipments of urgently needed supplies and equipment
- Establishing short-term courier routes to speed up delivery of lab tests
- Setting up shipments of prescriptions and home healthcare supplies direct to patient homes, where needed
- Adjusting delivery processes for our carriers and couriers to account for safety and physical distancing.
OptiFreight Logistics also recently launched a series of training videos for new shippers and program users. These videos on our customer website are very helpful during the pandemic when on-site trainings have not been possible.”
Technology enabled MedSpeed to support the dynamic routing needs of its clients.
Enhancing safety
Ensuring the safety of staff at home, in the offices and on the road as well as customers is a shared priority among all companies. Many have instituted new or reinforced distancing, cleaning, PPE and other measures for added protection.
“Even though we are considered an essential business, we have made every effort to follow the CDC and state guidelines,” TRIOSE, Inc.’s Romanelli reported. “When possible, we had employees work remotely. We re-arranged our offices to provide proper social distancing. We provide masks and require employees to wear outside of their personal workspaces and/or whenever in close proximity to others.
“We have disinfecting wipes/sprays stationed around common touch points (office equipment, break room) and have hired additional cleaning services who perform deep cleaning/disinfecting services nightly. Doors are propped to reduce the need to touch door handles. We discontinued visits to hospitals, visitors to the office, large group meetings and made use of video conferencing.”
While St. Onge Company switched to total remote work.
“Our offices are closed and our staff is working 100% remotely,” O’Neill said. “Meetings are facilitated through Zoom and conference calls. We have invested and created some processes and technology solutions to facilitate onsite operations discovery, data collection and analysis remotely.”
In addition to social distancing, PPE and cleaning practices, Ryder put into place contact-free deliveries.
“Following CDC guidelines for social distancing, Ryder has instituted contactless service at its maintenance, fuel and rental truck locations, as well as for road call and mobile maintenance services,” Martin stated. “Through these services, we work with customers to deliver the services they need while limiting contact to protect our customers, drivers, and our employees. Additionally, in the warehouses we manage, we continue to follow all global health authority guidelines for cleaning and disinfecting workspaces and common areas, as well as mandates for social distancing and the use of personal protective gear. We continue to secure disposable face masks, hand sanitizer, and cleaning supplies to our frontline locations throughout the Ryder network.
“OptiFreight Logistics also is working to adjust the protocol of deliveries.
“From a business perspective, we have seen health systems rapidly adapt their ground operations to serve more patients,” Laber shared. “We have also been working with our national carriers to change how they enter buildings, where they pick up and drop off packages, scheduling contactless deliveries, etc., in an effort to ensure patient care and to keep delivery drivers safe.”
Overcoming obstacles and making on-time deliveries
The pandemic has driven home the disruption to healthcare supplies, public safety concerns and routines of shipping.
“With the onset of COVID and limited supplies of inventory, delays are inevitable, which creates the need to source alternatives,” addressed Watson of St. Onge Company. “One consideration is how freight costs increase as hospitals begin acquiring supplies through non-distribution channels and rush orders. Costs increase on freight, minimum order fees, etc. In previous nationwide shortages (e.g., syringes and IV fluids), the need to go direct to the source was mission critical to survive.”
Many companies have faced challenges with getting deliveries out quickly.
“In the beginning of COVID-19, we were extremely restricted regarding deliveries and entering certain offices and facilities,” shared LeeSar’s Bowden. “This initially posed a challenge we overcame to maintain fast delivery times, as some offices were not allowing entry and were requiring drivers’ temperatures to be taken and other safety measures during deliveries.
“Also, in the beginning, we were immediately providing PPE and desperately needed supplies to multiple offices and locations, including member hospitals’ patient-positive areas where individuals were being quarantined for the virus. We continue to deliver PPE, masks, hand sanitizers and other supplies as needed by all member hospitals, urgent care and medical offices.”
Having a clear sight into shipment trajectory is a key factor to meeting urgent delivery needs.
“With shortages throughout the supply chain, it has become more important than ever for providers to have visibility into what product is coming into their facilities,” VPL’s Carroll noted. “Based on customer requests, VPL fast tracked the development of a “track and trace” technology solution that allows our customers to see when they will be receiving the vital product they have on order. As our customers work to ramp up elective procedures, having visibility into when they will receive product gives them time to work around shortages or delays in delivery.”
A new RyderShare logistics platform recently rolled out to help gain a direct and ongoing look at shipments.
“RyderShare integrates multiple transportation and warehouse management systems into a single platform that enables everyone moving goods through a supply chain to easily see potential problems and inefficiencies, collaborate in real-time, and take immediate action to course-correct,” Martin reported. “For example, we have a customer who experienced massive surges in volume during the pandemic, which meant they had to double the amount of loads going to nearly 4,000 locations across the U.S. Before RyderShare, it would have been impossible for them to calculate new delivery ETAs across the network, let alone communicate it out to their locations via phone and email. With RyderShare, the platform automatically calculated the new routes, and the locations could easily see the ETA of their deliveries and even follow their trucks in real-time.”
Direct and ongoing communication with customers also helps keep shipping on track.
“Customers know they can call us for customized support anytime,” OptiFreight Logistics’ Laber stated. “In one recent situation, a large hospital had multiple ventilators they were donating on a “first come, first serve” basis. One of our customers in need of equipment contacted the onsite OptiFreight Logistics coordinator that evening at 8 p.m. and he quickly took action to arrange a courier service to arrive first thing the next morning. Thanks to the quick actions of our team, they were able to get the ventilators and deliver them to their regional locations in a matter of hours.”
Meeting urgent shipping needs while maintaining lower costs requires special coordination.
“When the pandemic began, we were inundated with STAT orders each time a specimen was drawn or PPE needed to be repositioned,” MedSpeed’s Crampton explained. “Urgent movements such as these are costly, but amidst a pandemic our customers did not have time to think about efficiency. We quickly proposed a scheduled cadence for each customer that would save time for the clinical team, increase quality and keep costs down, all while meeting turnaround time requirements.”
Still, Smith of LeeSar, sees a light ahead in the tunnel amid the crisis.
“We’re finally putting more than PPE and toilet paper on the trucks,” he noted. “Pickup and delivery of masks to be sterilized for frontline healthcare workers and providers kept two drivers busy seven days a week, but that program has come to an end and we’re getting to a ‘new normal.’ More supplies are being ordered and delivered, and our drivers have been asked to do anything they can to speed up the process within their workday.”
References:
1. COVID-19 Supply Chain Update: Importation of Vital Food and Medical Products, https://www.fda.gov/news-events/fda-voices/covid-19-supply-chain-update-importation-vital-food-and-medical-products
2. Coronavirus (COVID-19) Pandemic: Supply Chain Stabilization Task Force, https://www.fema.gov/fema-supply-chain-stabilization-task-force
Pandemic preparation
What healthcare supply freight, logistics and shipping experiences from COVID-19 might help you prepare for the next major health or disaster crisis? HPN shares these insights from industry professionals.
“Having helped our clients through natural disasters like Hurricane Sandy in the east coast of the U.S. and the recent flooding in Texas, we felt well-prepared for this ‘natural disaster.’ We did strengthen our airfreight and ocean capabilities to deal with the supply shortage. We expect these services to continue to be needed because many hospitals are going to source from multiple places and vendors to prevent the same shortages. This pandemic caused a worldwide shortage of supplies versus a regional shortage. In the case of a natural disaster, our focus would be on intercepting and helping relocate products to temporary locations where the hospitals can operate. In the case of a worldwide pandemic, our focus was on moving supplies for hospitals from places they had not procured from in the past.”
Gerry Romanelli, Chief Commercial Officer, TRIOSE, Inc.
“Most disruptions experienced by the US healthcare supply chain are caused by localized events. COVID-19 has created worldwide disruptions that, frankly, no one was really prepared for. Our hospital supply chain customers are currently being asked to do what seems impossible. Their revenue is down, staff have been furloughed, product is unavailable, and they must ramp up elective surgeries. Moreover, they are being asked to cut costs while continuing to deliver high-quality care. We have found that they require significantly more logistics support and visibility as they purchase more product outside of their typical channels.”
Don Carroll, Vice President, Business Development,
Vantage Point Logistics (VPL)
“It’s critical to have a supply chain partner with the assets and expertise to provide solutions that can help you flex with market changes, whether that’s planned seasonality or the unpredictable. Thankfully, we have amazing people that deliver for our customers on a daily basis, even during a pandemic.
Probably the biggest difference has been the safety precautions that are unique to the pandemic. When you’re responding to a hurricane and you arrive with a truckload of essential supplies, there are a lot of people to help you unload. In this case, we need to limit contact as much as possible. It has forced many industries, including logistics, to think differently and it has accelerated the discussion around digitization.
The pandemic has created a greater sense of urgency for real-time, end-to-end visibility in the supply chain. It’s no longer a nice-to-have. It’s a must-have.”
Steve W. Martin, Senior Vice President,
Ryder Dedicated Transportation Solutions
“There is now a recognition that hospital systems need to develop system-level inventory visibility and a disaster-preparedness inventory response strategy. This will include reviewing the supply chain from manufacturers through to patient needs. Hospitals and health systems need to evaluate their sourcing strategy to determine how to integrate non-traditional sources effectively as well as community outreach. ‘Crowd sourcing’ will lead to additional supply chain practices to effectively manage incoming materials and ensure product quality measures are achieved.”
Tom Redding, St. Onge Company
“Visibility across healthcare networks and not just within their own entities. Vetting and approval of secondary and tertiary vendor sources. Secondary or tertiary supplies to be available when needed. Some clients are exploring alternate ways to ensure mission-critical supplies are available, which may lead to increased pandemic/emergency preparedness stocks.”
Aimee Watson, St. Onge Company
“The rapid onset and uncertainty of this pandemic has created an extraordinary acceleration of innovation. We have seen competitors work together for the first time to consolidate testing, health systems form partnerships with manufacturers outside of healthcare and a number of incredible community initiatives. This time has challenged healthcare leaders to harness their collective creativity and resourcefulness, and they have done so.
COVID-19 has reinforced the value of coordinated contingency planning. We operate in states where natural disasters require emergency scenarios to be implemented rapidly. Having a plan in place allows us to respond more quickly. This planning, which included consideration of public health emergencies, gave us a head start. The duration of this event has called for ongoing adaptation.”
Jake Crampton, CEO, MedSpeed
“Having a very dependable staff has been my saving grace. I’ve asked many of them to perform tasks outside of their normal scope of work, and each and every one has stepped up and done what was asked. It’s reminded me how invaluable good people are and that we really have an incredible team that can pull together to accomplish what needs to be done.”
Ronald Smith, Fleet Operations Manager, LeeSar
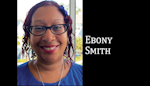
Ebony Smith
Ebony Smith was previously Managing Editor for Healthcare Purchasing News.