At one point in time not so long ago, tracking and tracing everything was more of a luxury, if not a novelty.
Today, it’s nothing short of a necessity, if not standard operating procedure by a majority of healthcare organizations.
Nearly five decades ago, bar coding insinuated itself into the pen-paper-clipboard procedural triumvirate, proving to be more efficient – even when sticky notes emerged a few years later.
The turn of the millennium, however, saw the rise of multi-dimensional bar coding (2-D and 3-D to start) and radiofrequency identification (RFID), the latter of which became a prominent modality within the overarching category of Real-Time Location Systems (RTLS).
Primary RTLS signal modality options include RFID via Wi-Fi or Ultra Wide Band (UWB), infrared (IR), ultraviolet (UV) and ultrasound (US). The emitted signals move through active, passive or hybrid chips or sensors on wireless networks.
All of this presents a plethora of choices for healthcare organizations – supply chain in particular – as well as strategies and tactics for how to adopt and implement these technological selections. For example, should a healthcare provider organization go all-in on one particular signal modality for tracking and tracing people, processes, products and equipment? Or should they apply specific signal modalities to certain tasks in a nod to a “best-of-breed” philosophy and which functional signal transmission vehicle makes the most sense?
Scanning the landscape
Technically, RTLS can be separated into three or more categories, according to Shawn McBride, Vice President and General Manager, Cardinal Health WaveMark.
McBride categorizes RTLS as real-time tracking of people (employees, patients, and visitors), real-time tracking of capital assets (wheelchairs, beds, infusion pumps), and real-time tracking of one-time-use supplies (stents, balloons, implants, sutures). “Each of these different categories can be accomplished with several technologies, and some technologies are more suited than others to each category,” he said.
WaveMark specializes in tracking one-time-use supplies, according to McBride. “We are technology-agnostic, so we will use any technology that is appropriate for the workflows of our customers,” he said. “We have found that RFID is well-suited to tracking supplies, so we have developed expertise in multiple types of RFID, but we also capture data with bar codes, and we will continue to look for new and evolving technologies.”
One useful metric for determining the best technology for a use-case is the total number of entities to be tracked over how large a physical space, McBride recommends.
“For WaveMark’s medical device tracking, it is typically tens-of-thousands devices held in a relatively small area – for example, a storage room in the OR Core,” he noted. “For this, RFID is perfect because the transponders are low-cost, they are engineered to work smoothly in dense tag environments, they do not require line-of-sight, they don’t need a battery and they are small, so they don’t take up more valuable hospital space. These benefits result in enhanced, more efficient workflows for our end users. Examples include very fast, highly accurate cycle-counting, faster clinical documentation with reduced errors, more efficient exception management of products including areas of product reordering, identification and finding missing products, and expiration and recall management.”
McBride acknowledges that facilities might want technology capable of tracking hundreds of people throughout an entire hospital.
“For this use-case, it is okay for the transponders to be a bit bulkier, it is okay for them to be higher cost – because you don’t need 10,000 of them – and the system may benefit from having a battery inside of each transponder so they can communicate at longer distances,” he said. “Understanding these constraints leads to the possibility of using many different technologies, including Wi-Fi beaconing, low-energy Bluetooth, IR, ultrasound, active RFID, passive RFID (no battery) or any of several others. Each of these has its own advantages driven by matching the capabilities of the technology to the requirements of the use-case.”
In addition to tracking people, RFID is key to tracking workflow and fortifying the documentation process, according to McBride.
“It’s hugely beneficial to optimizing your staff supply chain and optimizing your product and supplies inventory tracking with real-time status updates,” he said. “RFID also supports clinician documentation at the point of care by automatically recording product details used on a patient into their record and ensuring the appropriate documentation steps are taken during a surgical procedure. Because RFID provides visibility to a product throughout its lifecycle within the health system, RFID can also help alert management to issues with staff workflow compliance. For instance, if a product isn’t being documented as ‘used’ at the point of care but has gone ‘missing’ from inventory, you can identify the last place the product was ‘seen’ and what case it should have been associated with. This visibility allows you to mitigate when human error occurs and document appropriately.”
Big picture
“At Terso we see RFID-enabled inventory management, RTLS, patient tracking and the numerous automation opportunities to be part of a broader digital transformation called the Real-Time Healthcare System (RTHS).”
Pleshek describes this RTHS vision as arising from the fundamental need to improve access to care, patient safety, efficiencies and lower costs. He sees it as enabled by Internet of Things (IOT) technologies as well as an increasingly mobile, connected, collaborative and remote workforce.
“RTHS disrupts the classic care delivery model by using real-time information and communications to be more proactive and less reactive,” he said. “The key aspect to the RTHS is situational awareness – knowing the location of people (patients, clinicians, and care team members) and resources, such as medical devices and equipment, at all times during the patient experience. The concept of situational awareness involves sensing, collecting, analyzing and using state and event data to proactively reduce response times, introduce efficiencies, adjust priorities and match resources with demand to improve service levels.”
Pleshek labels location-aware technologies, such as RFID, RTLS and GPS, coupled with cellular, Wi-Fi and Bluetooth capabilities, vital to achieving situational awareness because they are able to determine the geographical position of a person or thing.
“Aside from being able to track the exact location of a patient, a doctor, or an asset such as a ventilator, many of these same technologies can be used to monitor temperature, humidity, light, movement, low-battery situations and hygiene complaint areas within hospitals,” Pleshek continued. “The RTHS uses up-to-date information from these technologies to remove delays in the management and execution of critical business processes including inventory management, asset tracking, patient and staff tracking, facility utilization and scheduling to name a few.”
Terso leverages RAIN RFID passive technology to help healthcare providers track products and assets throughout their facilities by creating situational awareness about each item, according to Pleshek. This includes location, condition (e.g., temperature), clinician usage and expiration date alerting.
“RFID provides a standards-based and proven technology solution for many items especially high-cost inventory and assets,” he said. “While RFID is a great fit for many applications, we believe additional ‘best of breed’ sensor technologies play an important role in realizing the benefits of the RTHS.”
In context of the RTHS, Pleshek recommends that healthcare providers develop a clear and comprehensive understanding of the most important requirements and use cases that contribute to operational efficiency, care quality and a positive patient experience as they make their decisions. Once these requirements and use cases are understood and prioritized a road map for the deployment of location and condition sensing technologies, like RFID, can be established and implemented, he adds.
Assessing possibilities
RFID may be a clear and popular choice for RTLS applications, track-and-trace technology experts also provide insights to other options in the electronic toolbox.
Williamson sees Bluetooth Low Energy (BLE) as a viable option, too.
“When comparing it to passive RFID, the tag cost is higher, but the infrastructure needed to grow is much lower,” he noted. “BLE also offers the advantage of covering more area if proximity is a concern. That being said, highly accurate, room-level visibility is more of a challenge when using BLE over RFID, although developments are being made to improve this.”
For tracking processes, products and workflow, however, Williamson still favors RFID.
“It can help support motion tracking through transition points and is ideal for processes that move through the same choke points or are limited to a smaller area where fixed infrastructure or mobile readers are being deployed,” he said. “The same can be said of RFID being used to track products, especially when tag cost and lifespan is considered. Long-term assets or disposable inventory both benefit from the use of RFID tags when compared to more expensive tagging solutions that only last 1-2 years. Additionally, room-level visibility is rarely essential when tracking assets. This allows for a smaller deployment of fixed RFID readers supplemented by mobile handheld readers, reducing the cost of infrastructure while enabling hospitals to optimize their asset management efforts.”
Snowday indicates that RFID represents a broad term that encompasses several technologies with a wide range of suitability for locating people.
“WiFi RTLS, for example, is only accurate at the zone level,” he noted. “Without adding supplemental technology, such as IR or ultrasound, it is typically not used for people. Bluetooth Low Energy (BLE), however, is a newer RFID technology that shows promise in this regard. While BLE is still considered an emerging technology as it relates to RTLS, advancements are being made to broaden its applicability for the workflow applications typically used when locating people. Although currently less accurate than technologies such as infrared, the great benefit of BLE is its lower effort and cost to implement. BLE is a widely accepted standard. Advantages of BLE also include the economy of scale, integration possibilities and the ability to locate with it at a lower price point.”
Snowday encourages giving IR a look.
“Infrared can quickly and definitively locate a person to the room or sub-room level and is highly suited to any use case where location certainty is necessary,” he said. “Nurse call automation (clearing patient calls when the nurse walks into the room) and patient flow applications (where patient-provider interactions drive automation and process improvement reporting) particularly require the highly accurate location data that IR provides.”
Snowday offers mixed reviews of RFID and IR in terms of tracking processes – including workflow.
“Various RFID technologies offer a wide variety of location accuracy, from the zone-level accuracy of Wi-Fi RTLS to the more precise accuracy of BLE,” he noted “Many RFID technologies are not granular enough to manage real-time workflow or document reliable location metrics for performance improvement. However, advances are being made with BLE and other RF-based solutions that may prove useful.
“IR is much more accurate for tracking processes than most RFID technologies since it is very resistant to generating false positives,” Snowday continued. “When tracking processes and automated workflow, it’s helpful to have room-level or better certainty when one or more tags are in a room or the same location.”
For tracking products, Snowday favors RFID.
“Small and inexpensive, passive RFID tags can be attached to products and discarded when no longer needed,” he acknowledged. “Although you can passively scan a device while it moves through a process, your range of applications are limited. Also, the expense of the readers/scanners needs to be taken into account, especially for use cases that require a large number of chokepoints.”
RFID may be more suited for equipment tracking, too, according to Snowday.
“Wi-Fi as an RFID technology has been available for years and has been a popular choice for tracking equipment,” he observed. “However, its zone-level granularity can limit its use. For example, nurses typically won’t use a Wi-Fi-based locating system as the location data isn’t reliable enough to provide value in the fast-paced nursing workflow. We recently launched a BLE asset tracking solution that has the lower-cost benefits of RFID technology with near-room location accuracy that both biomedical and nursing teams can use.
“For a use case that requires lower levels of location accuracy, but higher accuracy levels around doors (e.g., patient protection), organizations would be best suited to deploy a Wi-Fi-enabled tag with low-frequency chokepoints to notify staff when a patient has entered an area or doorway that the software has determined they should not enter,” Metzler advised. “For a staff-focused use case (e.g., staff duress), organizations only need tags and Wi-Fi because the system can alert a security guard within a few meters where the staff member is located when they activate their duress button.
“The tags are also designed to go into a higher accuracy mode when the duress click occurs, which further improves their accuracy,” he continued. “This type of deployment is cost-effective and fast, which lends itself to an efficient rollout to respond to the needs of organizations that require this type of system on an abridged timeline.”
Metzler points out that other technologies have a much higher technical lift so the projects are extended beyond the ideal time frame that an organization would need such a system in place following an incident.
Sounding off
Ultrasound can be a viable selection, according to Metzler.
“For a use case, such as nurse call or patient flow, we would recommend utilizing ultrasound (US),” he recommended. “These use cases require room- or bay-level accuracy and fast result of room entrance (sub-7s), which US can provide with the least amount of environmental interference.”
Metzler cautions that location services for visitor management remain a work-in-progress and an emerging market. Why?
“Primarily because of the challenge presented by a hospital-owned RTLS device given to the public,” he said. “Whatever device is chosen is very likely to be lost when visitors leave the facility. Given this challenge, passive RFID and BLE are the technologies in the market currently which are seeing some success. As these technologies mature in the RTLS space, we expect this area to grow significantly.”
Wi-Fi-based RTLS may be the most applicable for products and equipment, according to Metzler, even as RFID-equipped cabinets remain prominent for product storage and tracking.
“Organizations would use Wi-Fi-based RTLS to get an approximation of the location of the device (within several meters) alongside integration into the device vendor’s system to get context into what the device is doing,” he said. “For example, this combines ‘what is the tracked item doing’ with ‘where is the tracked item’ functionalities to determine if it should be moved to another location. This information would then be provided on an on-demand or periodic basis to the appropriate individual who would move the item. In our experience, this is typically sufficient to fine equipment, too.”
Still, ultrasound can serve a useful purpose.
“Organizations would employ [US] when the use case required a [higher] degree of accuracy, such as PAR level or nurse call to know with 100% certainty that a tag was in a specific room,” Metzler added.
Seeing red, infrared
In fact, for tracking people and processes, Paroda finds IR makes much sense.
“Infrared is the best-in-breed choice when it comes to locating staff, patients and visitors,” he noted. “In healthcare, the ability to quickly and accurately locate a team member or patient is of the utmost importance. IR allows for room location insights without the signal hopping and creating difficulties for the user to determine if an object is on one side of a wall or another. The near-100% accuracy makes it possible to accurately monitor contact tracing, patient/provider interactions and staff safety. Locating a patient, staff member or visitor to the right room in 5 seconds or less is crucial for use-case solutions to be effective.
“Similar to locating people, process monitoring requires discrete knowledge of exactly what occurred, the precise steps taken and in what order,” Paroda continued. “An IR solution offers certainty and low latency. This combination allows team members to know exactly which workflow steps occurred and how to proceed. IR also provides the ability to segment rooms or areas into discrete zones with high accuracy.”
For products and equipment tracking, however, Paroda favors the incorporation of RFID.
“Low-cost products are generally best tracked through RFID to minimize the expense, but high-dollar value products like artificial joints and other expensive consumables should be tracked with a technology that can provide certainty, especially if the inventory is running low,” he said. “Some RFID solutions can provide this but not all, occasionally making a solution like IR necessary.”
Paroda prefers a combination of modalities for tracking equipment.
“Equipment monitoring and management can often be accomplished effectively by using a mix of solutions, such as RFID and IR,” he indicated. “While some key locations like supply closets, clean rooms and dirty rooms may need the more complete coverage from IR, RFID can generally be used to cover broader areas by giving an estimated source of location for a lower cost and ensure that the entire facility is covered. When it comes to equipment, a combination of RFID and IR represents the best value approach when implementing equipment management.”
More on RTLS:
Tag-time: Chipping away at signal transmissions
RTLS cultivates accuracy, safety and security of data, people and products
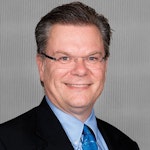
Rick Dana Barlow | Senior Editor
Rick Dana Barlow is Senior Editor for Healthcare Purchasing News, an Endeavor Business Media publication. He can be reached at [email protected].