Making product decisions without CS input; too embarrassed to ask questions
Submit your questions: email: [email protected]
CS Solutions
QIn today’s world, companies sell at a higher level to the hospitals and IDNs. As a result, changes for all sorts of products are “dictated” down the chain of command at all the system’s facilities. Many times, this “sale” includes the bundling of multiple product lines and related services in order to get a bigger piece of the pie and better price breaks. Many CS or OR Managers have changes coming their way simply because a sale was made at the corporate materials management level or even the CFO level without any input from the department managers. How can the CS or OR manager become a key part of the evaluation and selection process? What methods are effective in standing up for the department which is ultimately responsible for staff and patient wellbeing and safety? Haphazard products and brand changes can present a rippling effect of adverse events caused by incompatible products with ineffective performance. How can a department still fight for the brands that give them the best performance? Does quality still matter or is “barely acceptable and saves us 5 percent” going to be the new standard?
A The spiraling cost of providing healthcare has reached an all-time high and at the same time reimbursements for services are under tightening economic programs, which has resulted in diminished financial resources for operating our nation’s hospitals. Many hospitals have been forced to close as a result of their failed financial viability. Many other hospitals have merged and/or formed networks in an attempt to pool and conserve resources with a goal to be more financially solvent and survive these changing and turbulent times.
After labor, material resources are the largest expense of hospital operations and thus, when prudently managed, can yield great savings allowing the entity to prosper and sustain. Corporate organizational structures, including an executive asset or materials manager, have proven very successful in attaining goals and objectives and improving financial performance. I have yet to see any hospital mission statement that does not include intentions for providing high quality standards of care or preserving patient safety and welfare. The challenge lies in providing the best level of care for the right cost. Reality and good business practice dictate that economics must also be kept in the forefront, if an organization doesn’t produce a reserve and maintain financial operations in the black, it will be forced to close. As a discipline, material management comprises scientific principles and requires expertise and special skills in applications.
While it may be true that this management function has been moved to the corporate level, this should not exclude the input or consideration of subsidiary institutions or specialty departments. Product standardization, utilizing prime vendors, and bundling products and services can offer sizable savings to a healthcare system. However, it is not wise to make any product decisions or changes involving patient care that does not include a careful assessment, evaluation or approval of appropriate clinical representatives or other operatives. A successful corporate materials management structure should include a corporate product evaluation committee representing the various hospital divisions with ad hoc specialty departments invited to participate as appropriate. Members of the standing corporate committee should represent designated entities within the various hospitals and communicate with them in all appropriate matters.
For example, a member on the corporate committee may represent infection control and central service in such a case there may be a subcommittee of CS specialist pulled together from the various hospitals to review proposed sterile packaging changes. Minutes of corporate meetings and notices of proposed product changes should likewise be circulated to appropriate operatives to allow comments and feedback. If OR or CS managers feel they are not being included in important product decisions, which have affected their departments operations, they should jointly petition corporate materials management, outlining their concerns in a professional manner, and request a member be appointed from one of the hospitals to represent them.
Many behaviors have had to change in response to financial pressures. In honesty, we all know that in the past many product decisions were made from personal preference, brand loyalty, or based on want verses need. In the evaluation of proposed product changes, it is more important than ever to maintain objectivity and price must be a major consideration without compromising patient care. Even a 5 percent savings can have a significant impact on operations, but not at the expense of putting a patient in danger. Risk factors and associated outcomes can and should also be considered prior to deciding and some risks may be worth the potential savings.
The patient must always come first and if you believe a product that is being used in your department is inferior or poses a potential danger to quality patient care or employee safety, you are obliged to report this. You’ll need to do your homework, get the qualitative and quantitative facts, and present them to the appropriate sources or councils in your hospital. You can include or solicit the support of infection control, risk management, safety department, occupational health, legal services, or any other appropriate source in your hospital or network. You can also work through your representative on the corporate standardization committee or even request to be invited to a corporate committee meeting to present your case.
QI am new to the job and attended an in-service on infection control taught by another tech at my hospital. She was talking about causative agent and I was confused but too embarrassed to ask what she meant. Can you explain this to me?
A First off, welcome to the exciting world of sterile processing! This is a very dynamic, important, and broad field of study where there is always something new and exciting to learn — even for old dinosaurs like me. No one knows it all. Never be embarrassed to ask questions. As you progress in the field you will see that most of the work we do is detailed, precise, and must be done perfectly. Errors can have an adverse effect on patient care and safety. Always speak up.
Now to answer your question, a causative agent is the first link in the chain of infection –a pathogenic (disease)-producing organism such as a germ bacteria or virus. If the cleaning, disinfection or sterilization process is not performed effectively and the pathogen(s) are not adequately removed or destroyed, they can be transferred to patients and healthcare workers.
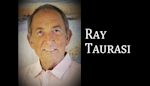
Ray Taurasi
Ray Taurasi is Principal, Healthcare CS Solutions. His healthcare career spans over five decades as an Administrator, Educator, Technologist and Consultant. He is a member of AORN, SGNA, AAMI and a past president of IAHCSMM. Taurasi has been a faculty member of numerous colleges teaching in the divisions of business administration, nursing, and health sciences. He is the author of numerous articles and textbook chapters; he is a frequent speaker at national and international healthcare conferences.
Note to readers from Ray Taurasi - In 2021, my life’s career path will transition to one of new opportunities and adventures. As a result, after nearly 19 years and 225 CS Solution columns, this edition will be my last.
“All changes, even the most longed for, have their melancholy; for what we leave behind us is a part of ourselves; we must die to one life before we can enter another.”– Anatole France
I wish you and your loved ones a healthy and joyful holiday season and a beautiful New Year! God Speed, Ray
https://www.facebook.com/pages/category/ Local-Business/Healthcare-CS-Solutions-128857 3061153887/ • email: [email protected]