Clearing the air on sterile storage, instrument positioning
Q
The other day I saw some cardboard shipping boxes in our sterile storage area. Is that an acceptable practice?
A
As with any practice in Sterile Processing & Distribution (SPD), there should be a standard -operating policy (SOP) in place that addresses sterile storage and acceptable practice for your facility. External shipping cartons and boxes are considered dirty because they have been exposed to unknown conditions. The shipping boxes can serve as generators and reservoirs for insects, dust and other contaminants.
ANSI/AAMI ST 79, section 3.3.6.5 discusses this topic and even suggests having a breakout area/or room located near or adjacent to a surgical or supply processing department. Having a breakout area helps to reduce the introduction of dust, insects, and other contaminants to this supply area.
In my view, it is not an acceptable practice to have cardboard shipping boxes in sterile storage. This should be addressed using your healthcare facility’s process for improving poor practice.
Q
We had a pre-audit survey to prepare for an upcoming survey. The person doing the survey told us that all hinged instruments must be in the open position for sterilization. They looked at our peel pouches and found many instruments not in the open position. Could we get cited for not having them all in the open position?
A
First, you should have an SOP on this topic. But, my answer is yes for the following reasons.
In September 2018, The Joint Commission, one of the premier surveying agencies, put out a notice stating, “They will also review peel packs to see if items that are awaiting sterilization or have just been sterilized are in the unratcheted position.” This could be why your surveyor brought this to your attention.
The new third edition of ST79:2017 now offers clearer guidance on the placement of instruments. Previous editions stated that instruments should be held open and unlocked; this guidance resulted in confusion because some surveyors thought it meant the instruments must be held wide open. In the new version of ST79, the committee eliminated the word “open” to alleviate the potential for confusion. It now states that “ratcheted instruments should be unlatched. Racks, pins, stringers, or other specifically designed devices can be used to hold the instruments in the unlatched position.”
So, what is a ratchet? It is a step-locking device on surgical instruments. As the handles are closed, the jaws are also closed and the ratchet holds them in a locked position. The ratchet consists of a notched bar on each handle. The notches are facing and overriding when the handles are closed. A ratchet on a medical device is considered closed once the first (step locking) ratchet is engaged; thus, if it is not engaged, it is considered open. So, you must make sure that ratcheted instruments are not engaged during the assembly process (See Figure 1).
Sterilization depends on the contact of the sterilizing agent with all surfaces for the prescribed time; thus, this can be achieved only if the sterilizing agent (e.g., steam) contacts all instrument surfaces. Hinged instruments, such as scissors and hemostats, should be sterilized in a position to ensure that the sterilizing agent can adequately contact all surfaces [(disassembled or unlatched per the original equipment manufacturer’s (OEM) instructions for use (IFU)].
We know that an OEM places wording in their IFU to give direction on this subject, so here is one example of an IFU from an OEM:
“for individual instruments with ratchet locks so instruments can be sterilized in an open position (unlocked) positions…instruments locked during autoclaving can experience cracked hinges (box locks) or other problems because of heat expansion…for instruments sets unlock all instruments and sterilize in the open position.” Miltex Surgical Instruments – Care and Handling (2005).
When making an SOP for your facility, it should reflect your practice. To do this, consider the various OEM IFU and standards to make the SOP. If you are audited, then you are “walking your talk” on this subject. Here is some possible wording that might be used in an SOP based on the information I have shared.
• “all ratcheted medical devices will be in the open, not engaged position during sterilization either in the natural, relaxed position or with the aid of a product to ensure it stays in the open position during the sterilization process. Also, other medical devices per the IFU that must be disassembled during sterilization will be.”
There are many companies that provide devices that help keep instruments in the proper position during the sterilization process. Work with them to make sure the products you use are clinically relevant and evidence-based for your process.
You want to get to best practice, and best practice is making sure all instruments that have a ratchet and instruments that need to be disassembled for sterilization are in the proper position so they can be properly sterilized, opened or disassembled. hpn
References
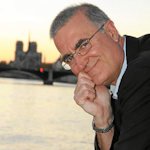
Stephen M. Kovach
Stephen M Kovach, BS, CFER, started in the medical field in 1975 as a sterilization orderly and has worked in many positions within the Healthcare Industry. He presently is Clinical Educator Emeritus at Healthmark, A Getinge company.